Understanding Near Miss Incidents: A Key to Safer Work Environments

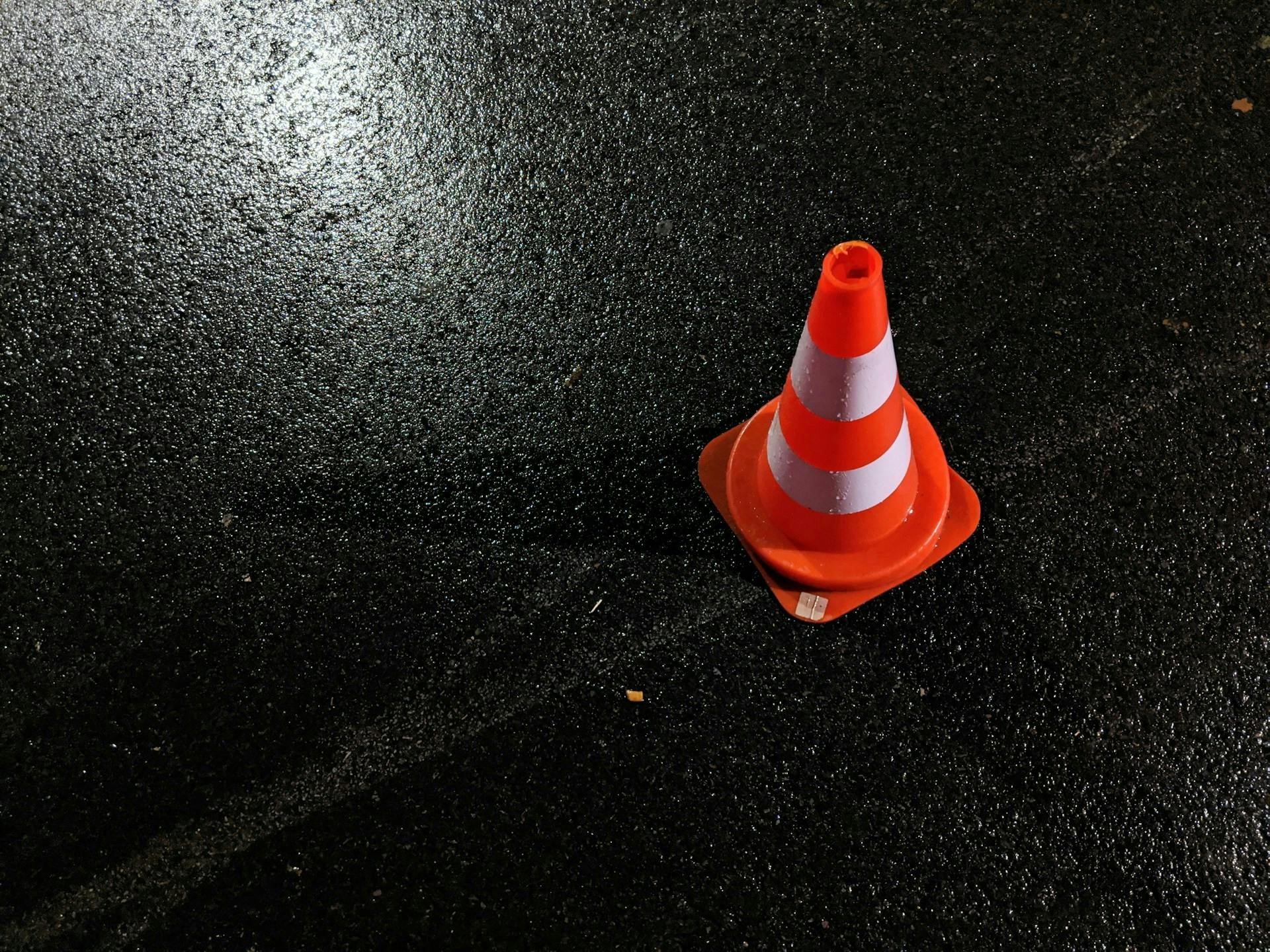
Every major workplace accident has a history. Often, it's a string of overlooked warnings; small mishaps, close calls, or things that “almost happened.” These are known as near-miss incidents, and they are among the most valuable yet underutilized tools in occupational safety.
In many organizations, safety programs focus heavily on responding to accidents after they occur. But near-misses are early indicators. Chances to intervene before damage is done. Think of them as the check-engine lights of the workplace. They reveal flaws in systems, procedures, or behaviors that, if left unaddressed, could lead to injuries, equipment damage, or worse.
Ignoring these signs means leaving safety to chance. Paying attention to them, on the other hand, can significantly reduce risk, strengthen your safety culture, and even save lives. From manufacturing floors to construction sites, near-miss reporting is one of the most cost-effective ways to boost hazard awareness, engage employees, and prevent future incidents.
In this article, we’ll break down what near-miss incidents are, why they matter, what causes them, and how to build a proactive reporting system that transforms these “almost accidents” into actionable safety improvements.
The Causes of Near-Misses
Near-misses act like warning lights on your safety dashboard. They provide an opportunity to learn without suffering the consequences of an actual accident. To prevent more serious incidents, it's critical to understand what triggers these close calls. The three main contributors to near-misses are human error, equipment malfunction, and environmental conditions.
Human Error in Near-Misses
Human error is the leading cause of near-miss incidents across nearly every industry. These errors typically fall into three main categories:
1. Unsafe Acts
Unsafe acts involve using improper techniques, skipping personal protective equipment (PPE), or taking shortcuts. These behaviors often result from:
- Complacency: The “I’ve done this a thousand times” mindset.
- Fatigue: Tired workers are more prone to poor decision-making.
- Lack of Training: Not knowing the correct procedures. This highlights the importance of using onboarding checklists and IT-supported training to close skill gaps.
- Rushing: Trying to finish tasks faster often leads to skipped steps or errors.
In industries like construction or excavation, this might involve operating machinery incorrectly, ignoring safety protocols, or working under inadequate supervision.
2. Communication Breakdowns
When team members are not aligned, the risk of a near-miss increases. Miscommunication can result in mistakes, especially in high-risk environments. For instance, in healthcare, communication failures account for about 31.9 incidents per 1,000 patient-days. Language barriers and translation errors further complicate communication. Improving how teams share information, especially across different languages, is essential to reducing these risks.
3. Decision-Making Errors
Some near-misses happen when workers misjudge hazards or overlook potential dangers. These errors often stem from rushing, overconfidence, or unclear instructions. A worker might underestimate a risk, skip a safety step, or assume conditions are safe without checking.
Equipment Malfunction and Near-Misses
Equipment failure is another major contributor to near-miss incidents. Some of the most common equipment-related issues include:
- Poor Maintenance: Equipment that doesn’t receive routine checkups can fail without warning.
- Design Flaws: Some tools or machines have structural weaknesses that increase their failure risk.
- Improper Use: Using equipment for tasks it wasn’t designed for raises the chance of malfunction.
In construction and industrial environments, these issues often appear as tool breakages, electrical system faults, or lifting equipment failures. These problems are more likely when maintenance schedules are skipped or delayed.
Regular inspections can help spot worn-out parts, loose fittings, or miscalibrations before they lead to incidents. Operators might notice unusual vibrations, strange noises, or reduced performance which are all signs that equipment needs attention. Recording these observations ensures the maintenance team can act before a failure occurs.
Environmental Conditions Contributing to Near-Misses
The work environment itself plays a major role in near-miss risk. Several physical factors can create hazardous conditions:
- Hazardous Surfaces: Oil spills, uneven walkways, or obstructed paths increase the chances of slips, trips, and falls.
- Tight Spaces: Working in cramped areas forces awkward movements or dangerous proximity to hazards.
- Weather Conditions: Rain, snow, ice, and high winds can make outdoor or partially enclosed workspaces much more dangerous.
- Poor Lighting: Inadequate lighting makes it harder to spot hazards, especially in precision-based tasks.
- High Noise Levels: Excessive noise can drown out warning signals and prevent workers from hearing instructions or alarms.
Most near-miss incidents are not caused by a single factor. They are often the result of multiple issues occurring at once. For example, a cluttered walkway might force a worker to take an awkward path while carrying equipment. Combined with poor lighting and unclear signage, this can lead to a trip hazard or improper tool handling. Language barriers can make matters worse by preventing clear communication about the hazard.
By improving training, maintaining equipment properly, and addressing environmental risks, organizations can significantly reduce the frequency of near-misses and avoid more serious incidents.
The Importance of Near-Miss Reporting
Near-miss reporting often sits in the shadow of accident reporting, yet it might be your most powerful safety tool. When workers report close calls, they provide invaluable insights into potential hazards before anyone gets hurt. That’s because these close calls are warning flares signaling more serious trouble ahead.
Reporting near-misses offers several benefits:
- Learning without pain: Near-misses teach the same lessons as accidents without the harm.
- Hazard spotting: They reveal hidden risks before they cause injuries.
- Future-proofing: Addressing issues found in near-miss reports prevents similar situations from becoming actual accidents.
- Building safety culture: When reporting becomes normal, safety becomes everyone's business.
- Saving money: Fixing issues found in near-miss reports costs far less than dealing with actual accidents—including workers' comp claims, lost productivity, and potential lawsuits.
Coupled with adherence to workplace safety protocols, near-miss reporting can greatly enhance workplace safety.
Implementing a Near-Miss Program: Step-by-Step Guide
Ready to build an effective near-miss program? This practical guide walks you through the process from start to finish:
1. Start with Clear, Shared Definitions
Before anyone can report a near-miss, they need to understand what qualifies as one. Use simple, relatable examples from your own workplace. For example, a ladder that slips but doesn’t fall, or a tool that narrowly misses someone during use. The goal is to make the concept concrete.
Bring definitions to life with visual aids, short videos, or printed pocket cards. Use toolbox talks and team meetings to reinforce understanding. Include these examples in your safety manuals and update them regularly based on new reports or feedback from the field.
It’s equally important to explain how near-misses differ from hazards or incidents. Supervisors should be trained to recognize the distinctions and help workers do the same. Invite input from employees during this stage—what they consider a “close call” can help refine your definitions and make the program more relatable.
2. Design a Reporting Process That Meets Workers Where They Are
The easier it is to report, the more likely workers will do it. Your near-miss reporting system should feel familiar, quick, and hassle-free, more like sending a text than filling out a form.
Consider offering multiple ways to report: a dedicated SMS number for text-based reports, a simple online form, and even a verbal hotline. Workers should be able to include photos or videos when relevant, and reporting should work on any device: phones, tablets, or desktops.
Multilingual access is also key. If you have a diverse workforce, make sure language isn't a barrier to reporting. Pilot the system with a few teams first to gather feedback on ease of use. You might find that workers prefer texting a photo and a short description rather than filling out a full incident form.
Once the process is live, revisit it often. Where do people get stuck? What do they avoid? Streamlining this process over time is part of what makes the system sustainable.
3. Train People to Recognize and Report Near-Misses
Awareness doesn’t come automatically, it needs to be built. That means training everyone, from new hires to seasoned team leads, on what near-misses are, why they matter, and how to report them.
Start with onboarding. Every new employee should understand your near-miss policy from day one. Then continue reinforcing it through regular training like quarterly refreshers, hands-on demos, or even monthly team huddles that include real examples.
Tailor training to specific roles. A warehouse associate and a maintenance tech face different hazards and will encounter different types of near-misses. Include real scenarios, encourage questions, and test understanding with short quizzes or role-playing exercises.
Supervisors play a crucial role here. Equip them to reinforce the message, answer questions, and model the behavior you want to see. If reporting isn’t championed at the management level, participation will stall.
4. Build a Culture of Trust, Not Blame
A near-miss program will fail if workers feel they’ll get in trouble for speaking up. From the beginning, your message needs to be clear: reporting near-misses helps everyone stay safe, and no one will be punished for doing the right thing.
Formalize this with a written, signed policy from leadership. Make it visible on posters, in training decks, and in every communication about the program. Translate it into the languages your team speaks, and repeat it often.
But trust isn’t built on words alone. It’s built on how reports are handled. If the first few employees who report get grilled or blamed, the system will go quiet. Train managers to respond with appreciation, not suspicion. Separate reporting from discipline, and protect workers from retaliation, especially in cases involving potential violations.
The more your team sees reporting as a sign of strength, not weakness, the stronger your safety culture will become.
5. Analyze Near-Miss Data and Identify Patterns
Reporting is only the first step. What you do with that information matters just as much.
Start by collecting consistent data on each near-miss: when and where it happened, what task was being done, who was involved, and what the potential outcome could have been. Use a standardized form or digital system to keep things consistent.
Then, look for patterns. Are most near-misses happening on a particular shift? At one location? With one type of equipment? Use dashboards or visual tools to make the data easy to explore. This helps you move from reactive to proactive, spotting issues before they escalate.
Pair near-miss data with your actual incident reports to find correlations. The same root causes often appear in both. And when you find recurring risks, dig deeper. Some trends will warrant deeper investigations or targeted training.
6. Develop and Implement Corrective Actions for Near-Misses
The power of a near-miss program lies in what you do with what you learn. For each recurring issue, develop a plan that includes:
- Engineering fixes that remove hazards altogether
- Procedural updates that clarify how tasks should be done
- Targeted training that addresses gaps in awareness or skill
- Communication improvements that close coordination gaps
Assign clear owners and deadlines to each fix. Use a shared system to track progress. Test any changes in a small setting first, and then roll them out more broadly once proven effective. Follow up to make sure fixes are implemented and working.
Most importantly, communicate these changes. When workers see that their reports lead to real improvements, they’re more likely to keep reporting.
7. Provide Feedback and Close the Loop on Near-Miss Reports
A near-miss report shouldn’t disappear into a black hole. Acknowledge every report, ideally with an automatic message confirming it was received. Then, follow up with updates as the investigation progresses.
You can go further by sharing summary dashboards with all employees, featuring key metrics and trends. Highlight specific examples—like a "Catch of the Month" or a short story showing how one report led to a hazard being fixed.
Offer regular opportunities for feedback on the reporting process itself. Are workers getting the support they need? Are they seeing results? Anonymous surveys or suggestion boxes can provide insight you might not get through formal channels.
Recognition matters too. Celebrate participation, not just outcomes. Even small acknowledgments, like shoutouts in a meeting, can reinforce that reporting is valued.
8. Evaluate Program Effectiveness of Near-Miss Reporting
Finally, step back and assess how the program is performing. Look at both the numbers and the experience.
Track metrics like the number of reports submitted, average time to resolution, incident reductions, and participation rates by team or department. Use leading indicators like reporting volume and not just lagging ones like injury rates, to spot shifts in culture and engagement.
Set clear goals for improvement. Compare results against industry benchmarks if available. Hold annual reviews with input from frontline workers, safety teams, and leadership.
Use what you learn to update training, refine reporting tools, and strengthen policies. The best near-miss programs evolve over time; they adapt to new risks, new technologies, and new workforce needs.
Using Technology for Enhanced Near-Miss Implementation
Modern safety programs benefit greatly from tools that simplify, accelerate, and scale near-miss reporting. Technology helps ensure that the right information reaches the right people, instantly, accurately, and without unnecessary complexity.
SMS based platforms like Yourco make this process easy and accessible, especially for non-desk workers. With the standard SMS interface, employees can report near-misses in real time using a tool they already use daily: text messaging. There’s no need for app downloads or training. Workers can submit reports immediately, attach photos, and communicate in their preferred language thanks to built-in translation support.
Here’s how Yourco enhances near-miss reporting:
- Instant photo reporting: Allows workers to take photos or videos on the spot and easily SMS it to their supervisor, attaching visual context to their report.
- AI-powered translations: Automatically translates messages into 135+ languages so diverse teams can report issues in the language they’re most comfortable using.
- Automated alerts and follow-up: Safety managers receive instant notifications when a near-miss is reported, allowing for real-time response and follow-up actions.
- HRIS & payroll integrations: Sync with 240+ HR and payroll platforms to route reports based on department, location, or supervisor—ensuring fast, accurate handling.
- Feedback collection via SMS surveys: Use quick polls and surveys to gather follow-up information or check on resolution satisfaction after an incident is reported.
- Real-time dashboards: Monitor near-miss trends, reporting rates, and resolution timelines across locations to identify patterns and prioritize corrective actions.
- Secure document and file sharing: Need to send a follow-up safety notice or inspection checklist? Yourco allows secure file links via SMS, with PIN-gated access for sensitive documents.
- Automated notifications ensure the right people are alerted the moment a serious near-miss is reported.
By combining accessible platforms like Yourco with intelligent tools and systems, organizations can turn near-miss reporting from a compliance task into a proactive safety asset—one that drives continuous improvement and strengthens the culture of accountability.
Safety Starts with What Almost Happened
Near-miss reporting is one of the most powerful yet underused tools in workplace safety. It allows organizations to learn from close calls instead of waiting for injuries or damage to occur. When reported, tracked, and acted upon, near-misses reveal patterns, expose blind spots, and give teams a chance to fix problems before they escalate.
But a successful near-miss program requires more than good intentions. It requires clear definitions, easy reporting methods, strong training, and—most importantly—a culture that encourages speaking up without fear of punishment.
That’s where tools like Yourco make a real difference. By using simple SMS-based reporting, real-time alerts, photo documentation, and multilingual support, Yourco removes the friction from safety communication. It meets workers where they are, on the job, in the field, and on their phones, and makes it easy to capture crucial safety information the moment it happens.
When safety tools are accessible, trusted, and integrated into daily routines, reporting increases. Engagement grows. And accidents go down.
Yourco helps turn near-miss reporting from a checkbox into a core part of your prevention strategy. One that empowers your frontline, supports your safety teams, and ultimately keeps your workforce safer, stronger, and more connected.
Try Yourco for free today or schedule a demo and see the difference the right workplace communication solution can make in your company.