12 Rules for Workplace Safety Every Manager Should Know

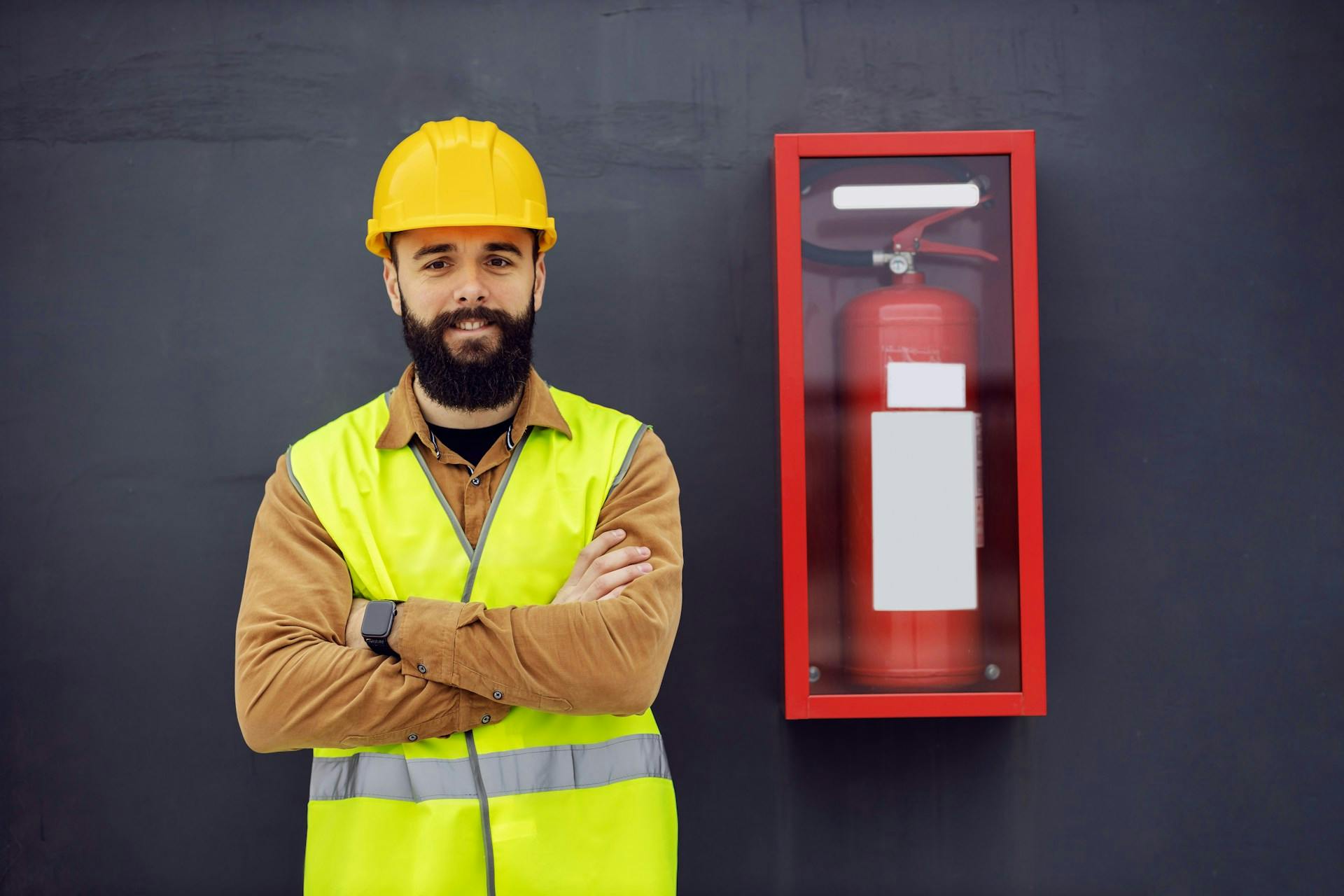
Behind every injury, slip, trip, and fall incident are real people facing real pain. Each incident represents a coworker dealing with physical suffering, lost income, and medical expenses, while your company absorbs overtime costs, production delays, and insurance hikes.
You can't bubble-wrap your workplace, but you can stack the odds in everyone's favor by making safety part of your daily routine. These 12 rules for workplace safety blend OSHA requirements with practical tactics that actually work. Use them consistently and you'll see the difference: fewer close calls, faster hazard reporting, and a team where everyone takes personal responsibility for keeping each other safe.
1. Implement Proper Safety Training and Documentation
Proper safety training is the cornerstone of accident prevention in industrial settings. Your program should combine a thorough onboarding process with regular refresher courses, focusing on role-specific hazards and emergency procedures.
Modern safety training increasingly incorporates advanced technology. AI-powered systems are now important for accident prevention, with many of construction leaders recognizing their importance in reducing workplace incidents. Consider integrating wearable technology and real-time monitoring systems into your training programs.
Document all training activities and maintain digital records of attendance, certifications, and competency assessments. Consider using an SMS-based employee communication platform like Yourco to deliver safety quizzes in multiple languages. Scheduled reminders for certification renewals and upcoming training sessions sent via SMS enjoy a 98 % read rate, which is far higher than traditional email.
For effective implementation, break down complex procedures into micro-training segments delivered through text messages. Use photos, written instructions, and interactive quizzes to reinforce learning, and track completion rates and comprehension through Yourco's analytics dashboard.
2. Require Proper Personal Protective Equipment (PPE) for Every Task
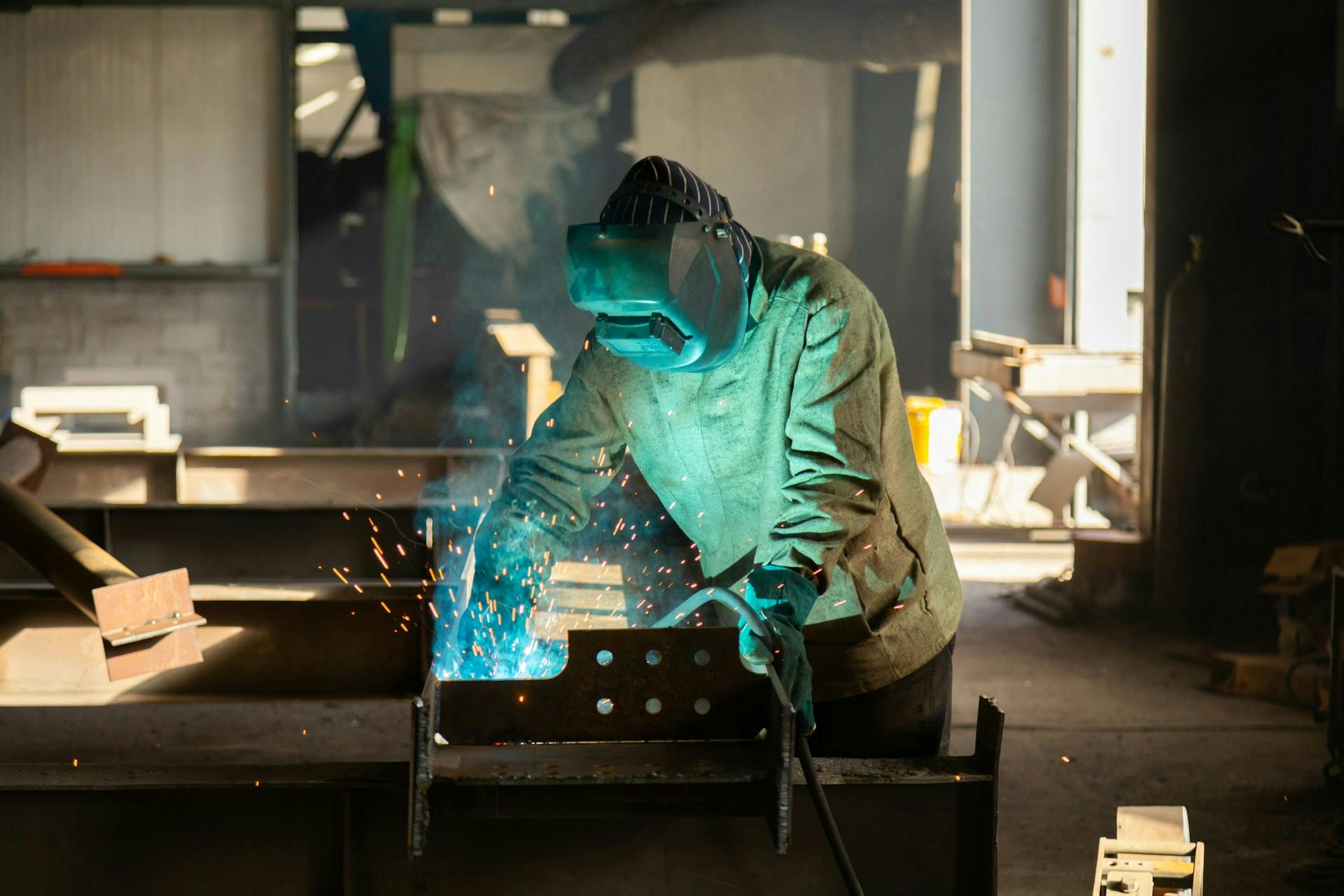
Flying debris, splashes, and equipment contact hurt workers every day. OSHA requires a written hazard assessment first, then you must supply and pay for all necessary protective gear. Hard hats, ANSI-rated eye and ear protection, cut-resistant gloves, hi-vis vests, and non-slip shoes cover the basics. Add respirators, chemical aprons, or arc-flash suits for specific hazards.
Providing equipment is just the start. Train everyone to properly fit, clean, and inspect each item. Replace damaged gear immediately and document everything to stay OSHA-compliant.
With Yourco, before shifts, you can send a quick text: "Team A: goggles and gloves for line-cleaning today", so everyone knows what they need. The rule stays simple: if the job needs PPE, the job waits until the PPE is on.
3. Maintain Clean and Organized Work Areas
Clean, organized workspaces prevent most slip, trip, and fall incidents. These accidents typically start with something as basic as a loose cable or unnoticed spill. Implement a "clean as you go" policy and ensure walkways and emergency exits remain unobstructed. Create a daily cleaning schedule that includes:
- Morning workspace inspection: Check for cords, wet floors, and blocked walkways before operations begin. Restock cleaning supplies if needed.
- Mid-shift cleanup: Clear clutter from shared areas like break rooms, equipment zones, and hallways. Wipe up any minor spills or debris.
- End-of-day organization check: Return tools and materials to proper storage, unplug unused devices, and take out trash to reduce overnight risks.
- Immediate response to spills or hazards: Mark the area with signage, clean it promptly, and report recurring issues to supervisors.
Sticking to this routine helps prevent injuries and keeps your team focused, productive, and aware of their environment throughout the day.
4. Establish Clear Emergency Procedures
Every facility needs robust emergency and safety procedures that take into account the mobile nature of non-desk workers. Map evacuation routes and assembly points for each area and designate trained safety leaders for every shift.
With OSHA's proposed Heat Illness Prevention Rule requiring employer-funded hydration stations and rest-break protocols for workers in environments above 80°F, ensure your emergency procedures address heat-related incidents alongside traditional safety concerns.
For operations spread across multiple locations, it's important to standardize your emergency procedures while accounting for site-specific hazards. Incorporating employee alerts through SMS communications ensures that critical information reaches your workforce promptly. Text messages boast an impressive read rate and quick response time, making them an effective tool for alerting employees about emergency protocols.
Consider using Yourco's SMS-based employee communication platform to safely deliver alerts and emergency notifications in multiple languages, ensuring clear understanding across your diverse workforce.
Conduct regular emergency drills. Use them also to test your emergency notification systems and identify potential gaps in your procedures. After each drill, gather feedback from your non-desk workers about what worked and what needs improvement.
5. Implement Proper Equipment Operation Protocols
Only authorized, properly trained personnel should operate machinery, and current certifications must be verified before access is granted. Follow manufacturer specifications, keep operator manuals handy, and never bypass machine guards.
Modern safety technology offers unprecedented protection capabilities. AI-powered computer vision systems can now analyze video feeds to identify safety violations. Consider implementing predictive maintenance systems that can forecast equipment failures before they occur.
Maintain a routine inspection schedule with digital tracking, and immediately remove malfunctioning equipment from service. Document all maintenance and schedule periodic operator recertification to keep skills current.
6. Create Hazard Reporting Systems
Offer multiple ways to report issues, including anonymous options and text-based solutions, so all workers can easily raise safety concerns. SMS-based reporting enables field workers to instantly alert supervisors about potential hazards without needing desktop access.
Recent studies show that 49% of workplace injuries go unreported globally, often due to inadequate training or fear of retaliation. This underscores the critical importance of creating accessible, non-punitive reporting systems.
Include automatic escalation for serious risks and a tracking mechanism for follow-up. Foster a no-blame culture, respond swiftly to reports, and communicate corrective actions to build trust in the system.
7. Enforce Proper Body Mechanics and Ergonomics
OSHA encourages training on proper lifting techniques under general safety guidelines, but no explicit federal mandate requires all employers to provide it. Before any physical task, a worker should take 30 seconds for quick stretches — reach for hamstrings, roll shoulders, rotate trunk. This loosens tight muscles and prevents those "I moved wrong" moments that ruin the day.
Train employees to lift with their legs, keep loads close, and use mechanical aids such as pallet jacks or lift assists for items over 50 lbs. Rotate repetitive tasks, encourage short breaks, and perform regular ergonomic assessments, especially in manufacturing and warehousing areas.
Also, advanced ergonomic solutions are becoming more accessible. AI-powered exoskeletons can reduce overexertion injuries in logistics, while wearable sensors can monitor posture and provide real-time feedback to prevent musculoskeletal disorders.
Encourage workers to report tasks causing discomfort and use their feedback to modify workstations or processes for better alignment and reduced strain.
8. Maintain Substance-Free Workplace Policies
Impairment slows reactions and clouds judgment, turning routine tasks into serious hazards. This hits hardest in jobs requiring precision and quick decisions, where transportation incidents cause 37 percent of workplace deaths. Your workplace needs a clear substance policy including testing protocols, Employee Assistance Program access, and fair disciplinary steps.
Train your team to recognize warning signs like slurred speech, unsteady movements, or alcohol odors, and build a culture where people feel comfortable reporting concerns. If you suspect impairment, remove that person from duty immediately, document the situation, and connect them with support resources. Make asking for help simple by setting up an anonymous text line, as sometimes a private message can prevent tragedy.
9. Schedule Regular Safety Audits and Inspections
Regular safety audits and inspections are your first line of defense against workplace accidents. Implement a structured inspection schedule that includes daily equipment checks, weekly area inspections, and monthly comprehensive facility audits. Use detailed checklists that cover all critical areas:
- Machinery conditions: Look for worn parts, exposed wiring, missing guards, and signs of overheating or malfunction.
- PPE availability: Ensure required gear like gloves, masks, helmets, or eye protection is fully stocked, undamaged, and stored in clearly marked locations.
- Emergency equipment accessibility: Confirm that fire extinguishers, eye wash stations, and first aid kits are clearly labeled, unblocked, and up to date.
- Proper signage placement: Check that all safety, exit, hazard, and instructional signs are visible, undamaged, and in the correct locations.
Document every inspection thoroughly, including photos of potential hazards and detailed notes about necessary corrections. Track completion of corrective actions to ensure nothing falls through the cracks. This thorough documentation provides a clear record for compliance purposes and helps identify patterns that might indicate underlying safety issues.
10. Develop Effective Safety Communication Systems
When lives are on the line, communicating safety protocols quickly is key. Utilize multiple communication channels, primarily SMS, since most of text messages are opened within 5 minutes. Digital displays in break rooms and physical bulletin boards can reinforce critical safety information.
Keep safety updates brief and frequent rather than lengthy and sporadic. For instance, send quick reminders about PPE requirements at the start of shifts or alert workers about specific hazards as they're identified. Consider implementing a dedicated safety hotline where workers can report concerns immediately.
11. Encourage Taking Scheduled Breaks to Stay Sharp
Working through fatigue causes more accidents than most realize. Skiping breaks cause the drop in focus, slower reactions, and routine tasks become more dangerous. Treat breaks like any safety protocol. For heavy manual labor, encourage 10-minute breaks hourly. For moderate tasks, workers should step away for 15 minutes every two to three hours. A genuine break means leaving workstation completely. That’s the time to stretch, hydrate, or get fresh air.
Yourco can send automatic break reminders so busy shifts don't become endless marathons. You might even set up quick fatigue check-ins to catch warning signs early. Stock break areas with water, healthy snacks, and quiet space where people can recharge. Your team will return sharper, more alert, and ready to focus on safe work.
12. Implement Safety Protocols and Monitor Compliance
Establish baseline safety metrics and set clear goals for improvement. Roll out new safety rules through a combination of formal training sessions and regular updates. Use visual aids throughout your facility and reinforce rules through daily toolbox talks.
Monitor compliance through regular safety audits and consider leveraging Yourco's polling features to gather real-time feedback from workers. You can announce survey results to foster engagement. Track key metrics such as:
- Incident rates: Measure the frequency of workplace injuries or safety violations to identify trends and areas needing attention.
- Near-miss reports: Encourage teams to report close calls, which often reveal hidden risks before they lead to actual incidents.
- Hazard identification submissions: Track how often workers report unsafe conditions or equipment issues to evaluate awareness and responsiveness.
Make adjustments based on collected data and employee input, carefully interpreting survey results to identify areas for improvement. Remember that successful safety programs evolve, so regularly review and update your rules based on new insights and changing workplace conditions.
Reinforce Workplace Safety Rules Company-Wide
Rules become habits through daily practice, not wall posters. Focus on leadership, training, and instant communication to make safety stick. Start with supervisors — when they begin shifts with safety checks or wear proper PPE themselves, your team gets the message that protection matters. Visible leadership support strengthens workplace culture and shows that prevention starts at the top.
Make training count with specific targets like "reduce slips and trips 25% this quarter" instead of vague promises. Track your results because engaged, well-trained teams experience dramatically fewer incidents. Regular toolbox talks and safety sessions help cut injuries and reduce absences when part of comprehensive safety programs.
Keep communication flowing in real time. Through Yourco, send instant multilingual alerts during weather emergencies, shift-specific PPE reminders, or collect photo evidence of hazards instantly. Every message gets automatically logged, creating searchable records for pattern analysis by location or shift. The dashboard highlights what matters, such as near-miss reports, response times, and training completion, showing whether your rules actually work.
Strong leadership, effective training, and instant communication transform safety from policy into mindset. Your team's morale and productivity will improve while accidents decline, creating a culture where everyone takes responsibility for sending each other home safely every day.
Want to see how seamless communication can power your safety culture? Try Yourco for free today or schedule a demo and experience the difference the right workplace communication solution can make.
FAQs
What are the critical elements to include in a workplace safety training program for non-desk workers?
A strong safety training program for non-desk workers should use scenario-based lessons that reflect real job hazards. Deliver training through accessible channels like SMS or mobile apps to reach field teams quickly. Encourage a culture of safety by supporting anonymous hazard reporting and ensuring swift follow-up. Regularly update the program based on feedback, tech advances, and regulatory changes.
How can wearable technology and AI-powered systems improve safety in industrial settings?
Wearables like smart helmets and wristbands track vital signs and environmental hazards, alerting workers in real time. AI enhances safety by detecting risks, monitoring video feeds for violations, and predicting equipment failures. Together, these tools create a proactive safety system that helps prevent accidents before they happen.
What are the best practices for setting up an effective hazard reporting system in the workplace?
Offer multiple, easy-to-use channels for reporting hazards—SMS, mobile apps, or hotlines—so all workers can participate. Build trust by promoting a no-blame culture and providing training on how to report effectively. Ensure fast follow-up, share improvements, and use data to guide safety decisions.
How can companies ensure compliance with OSHA's new regulations on PPE fit requirements?
Review OSHA’s updated standards and adjust your PPE inventory to include gender-specific, size-inclusive gear. Hold PPE fit testing sessions and train workers on how to spot and report fit issues. Use digital tools to track fit data, schedule reassessments, and gather feedback to stay compliant.
What strategies can managers implement to foster a substance-free workplace culture?
Create a clear, supportive substance-free policy and share it company-wide. Offer confidential help through EAPs, educate teams on substance risks, and use respectful testing when needed. Build trust by focusing on support over punishment, and encourage peer support networks to reinforce a safe, substance-free culture.