Mastering Warehouse Safety: Essential Tips for HR Managers

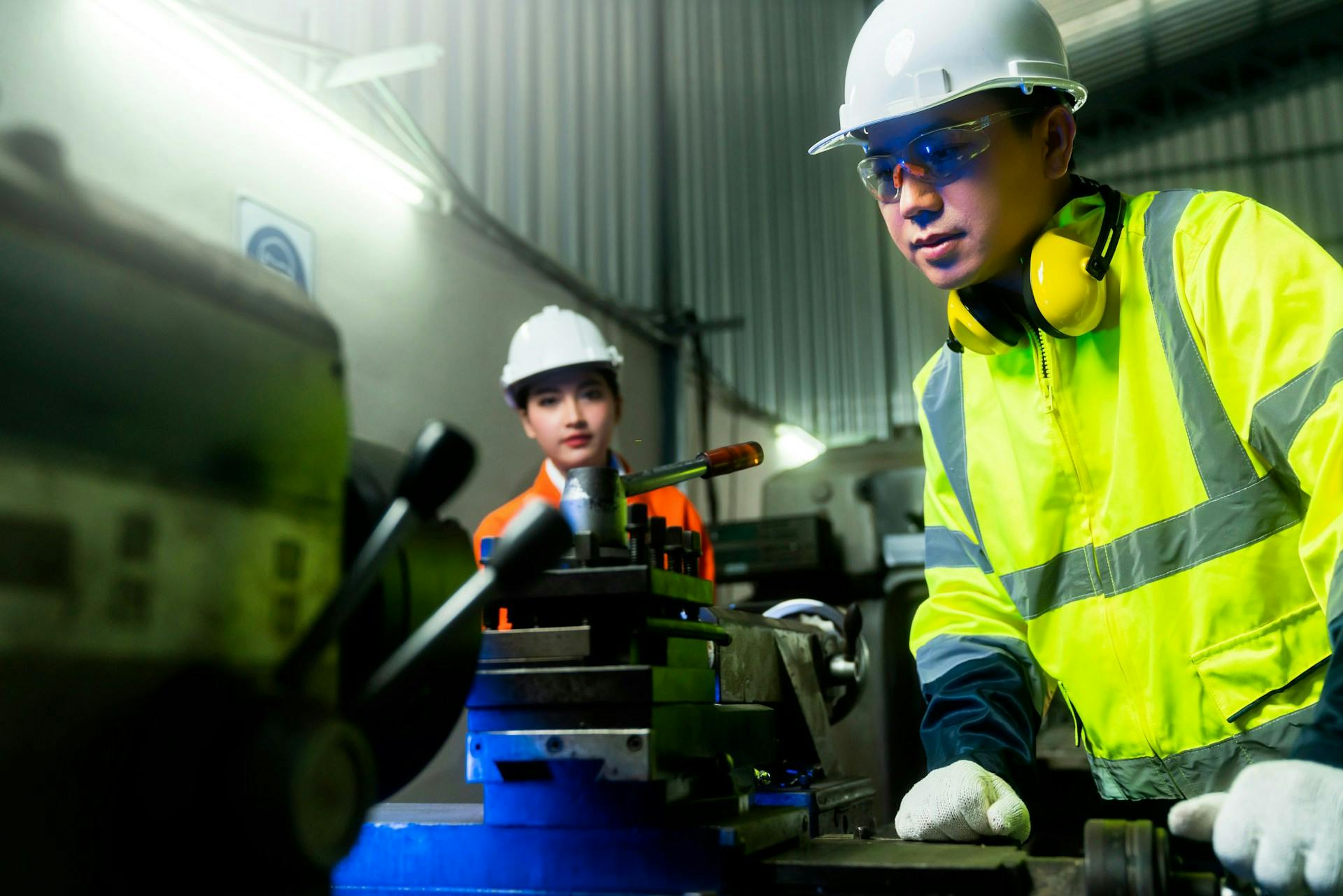
Warehouses combine heavy machinery, manual labor, and constant movement, creating an environment prone to accidents. With nearly 100,000 warehouse accidents reported annually in the U.S., solid safety protocols directly affect productivity, team morale, and profits.
According to the Occupational Safety and Health Administration (OSHA), unsafe use of forklifts is the most cited warehouse hazard, often causing serious injuries or deaths. Other dangers include slips, trips, and falls, manual handling injuries, falling objects, and hazardous materials. Implementing comprehensive workplace safety rules is needed to mitigate these risks.
Effective safety measures protect both workers and business operations. Injuries result in downtime, reduced productivity, and potential legal issues. A strong safety culture improves morale and retention as workers recognize that their wellbeing matters.
The Importance of Warehouse Safety
Warehouse accidents hurt workers and disrupt operations. The nearly 100,000 annual warehouse accidents in the U.S. include musculoskeletal problems from improper lifting, slips and falls, and forklift accidents. These incidents reduce productivity and increase workers' compensation claims.
Strong safety programs:
- Reduce compensation claims
- Minimize downtime
- Improve productivity
- Enhance employee retention
Safety investments typically pay for themselves through fewer incidents and better operations. Companies with robust safety measures experience fewer injuries, lower insurance costs, and improved performance. Moreover, workers stay longer with companies that demonstrate commitment to their safety.
Regulatory Standards and Compliance in Warehouse Safety
Warehouse safety falls primarily under the Occupational Safety and Health Administration (OSHA) in the United States. OSHA provides a comprehensive set of standards and regulations that warehouse operators must follow to ensure a safe working environment. These standards cover hazard communication, material handling equipment, personal protective equipment (PPE), emergency procedures, and recordkeeping obligations.
Key OSHA Requirements for Warehouse Safety
OSHA regulations serve as the foundation for maintaining safe, compliant warehouse environments. Understanding these requirements helps businesses protect workers, avoid costly violations, and build a culture of accountability.
- Hazard Communication: Employers must inform and train employees about hazardous chemicals in the workplace. This includes providing Safety Data Sheets (SDS) and proper labeling of chemicals.
- Forklift Safety: OSHA mandates that operators must be properly trained and certified. Regular pre-operation inspections and safe operating procedures are important to prevent accidents such as rollovers and collisions.
- Personal Protective Equipment (PPE): Warehouses must assess hazards and provide suitable PPE, such as gloves, eye protection, and high-visibility clothing. Regular training on correct PPE usage is also required.
- Emergency Action and Fire Safety: Facilities must develop and communicate emergency evacuation procedures, maintain accessible and marked exit routes, and follow fire suppression and prevention standards as per National Fire Protection Association (NFPA) codes.
- Lockout/Tagout (LOTO): Procedures must be in place to control potentially hazardous energy during equipment maintenance. This includes training and periodic audits.
- Ergonomics and Manual Handling: Training on proper lifting techniques and implementation of mechanical aids is essential to prevent musculoskeletal injuries.
Documentation and Reporting Obligations
Proper documentation and reporting are important aspects of regulatory compliance. Warehouses must:
- Maintain accurate records of workplace injuries and illnesses.
- Keep detailed incident reports and regular safety inspection logs.
- Comply with OSHA's injury and illness recordkeeping requirements, including the use of OSHA Form 300.
- Document all safety training sessions and employee certifications.
Beyond federal OSHA regulations, warehouses may also need to comply with state and local codes, particularly regarding hazardous materials storage and building safety standards.
Digital communication tools, such as SMS-based employee communication solutions, can significantly enhance compliance efforts. These tools ensure that all employees receive and acknowledge safety updates and training materials, creating an audit trail for regulatory purposes. They can also facilitate real-time hazard reporting and dissemination of important safety information.
A Deeper Look at Common Warehouse Safety Hazards
Warehouses are complex environments where various hazards can pose significant risks to worker safety. Understanding and addressing these common dangers creates a safer workplace for everyone. Let's explore the major hazard categories and strategies to mitigate them effectively.
Forklift and Vehicle Accidents
Forklifts are essential tools in warehouse operations, but they also present one of the most significant safety risks. Common incidents include overturns, collisions, and pedestrian impacts—often caused by poor visibility, speeding, or operator inattention.
To mitigate these risks:
- Ensure all operators are properly trained and certified, with refresher courses conducted regularly
- Implement clearly marked traffic lanes and pedestrian walkways to reduce interaction risks
- Install mirrors at blind corners, warning signs, and use proximity sensors or lights to alert nearby workers
- Conduct regular equipment inspections and preventive maintenance to catch mechanical issues early
Slips, Trips, and Falls
Slips, trips, and falls are also among the most common warehouse injuries, often leading to sprains, fractures, and lost workdays. Wet floors, loose materials, uneven surfaces, and inadequate lighting are key contributors. These incidents not only pose physical risks but also drive up insurance costs and reduce productivity.
Prevention strategies include:
- Regular cleaning schedules and immediate spill response procedures to minimize hazards
- Clear storage policies to keep aisles and walkways free from clutter or misplaced items
- Installation of anti-slip flooring, mats, or coatings in high-traffic or moisture-prone areas
- Adequate lighting throughout the facility, especially in corners, stairwells, and entryways
- Use of warning signs in recently cleaned or high-risk areas
Manual Handling and Ergonomic Injuries
Manual handling and ergonomic injuries are another cause of lost workdays in warehouse settings. Tasks that involve lifting, pushing, pulling, or carrying heavy items can strain muscles and joints, especially when performed repetitively or without proper technique.
OSHA highlights repeated bending, twisting, and overhead lifting as common risk factors. These injuries not only affect worker health but also increase workers’ compensation claims and lower productivity.
To reduce ergonomic risks:
- Offer hands-on training sessions focused on safe lifting and movement techniques
- Provide mechanical aids such as pallet jacks, forklifts, and conveyor systems to reduce manual strain
- Design workstations and shelving to minimize reaching, bending, or awkward postures
- Encourage regular breaks, job rotation, and stretching to prevent overuse injuries
- Conduct ergonomic assessments to adjust tasks and tools for safer use
Material Storage and Falling Objects
Improper material storage in warehouses can lead to serious injuries and operational disruptions. Falling objects from overstacked pallets, unstable shelving, or improper loading techniques pose risks to employees, especially in high-traffic areas.
For instance, Amazon fulfillment centers have highlighted incidents where inventory collapsed due to poor stacking practices. These accidents not only threaten worker safety but also result in damaged goods and costly downtime.
To reduce these risks:
- Establish clear stacking procedures, including maximum height guidelines
- Invest in heavy-duty shelving units designed for warehouse loads and conduct routine inspections for wear or instability
- Install guardrails, overhead protective barriers, and safety netting in storage areas
- Train all staff on safe storage techniques, including load distribution and securing items
- Use load labels to prevent overloading and ensure safe handling
Hazardous Materials and Chemical Exposure
Warehouses storing chemicals face unique hazards that can result in fires, toxic exposures, and environmental contamination if not properly managed. Even small leaks or spills can lead to serious consequences, including respiratory issues, skin burns, or long-term health complications for workers.
Regulatory agencies like OSHA and the EPA mandate strict chemical storage guidelines to prevent such incidents. To mitigate these risks, it’s important to:
- Clearly label all chemical containers with hazard information and expiration dates
- Segregate incompatible chemicals to prevent dangerous reactions
- Provide and enforce the use of personal protective equipment (PPE), such as gloves, goggles, and chemical-resistant clothing
- Install clearly marked and accessible emergency eyewash stations and showers
- Conduct regular inspections and maintain Material Safety Data Sheets (MSDS) for all substances
- Train staff on handling, spill response, and emergency evacuation protocols
Loading Dock and Conveyor Dangers
Loading docks and conveyor systems are some of the most hazardous zones in a warehouse, where a momentary lapse can lead to serious injury. Workers are exposed to risks such as falling from elevated dock edges, being pinned between vehicles and the dock, or getting caught in conveyor machinery. Inadequate safeguards, rushed operations, and poor visibility often contribute to these accidents.
To reduce risk:
- Install dock bumpers, guardrails, and dock levelers to prevent vehicle and pedestrian accidents
- Use visual floor markings to define danger zones
- Enforce strict lockout/tagout protocols before servicing conveyors
- Schedule routine inspections of dock and conveyor equipment
- Provide hands-on training for all personnel working in or around these systems
Building a Safety-First Culture in Your Warehouse
Creating an effective safety program in a warehouse environment requires more than just rules and regulations—it demands a culture where warehouse safety is valued at all levels of the organization. A safety-first mentality helps warehouses reduce accidents, improve productivity, and boost employee morale.
Leadership's Role in Warehouse Safety Culture
Management plays a decisive role in establishing and maintaining a safety-first culture. When executives and supervisors demonstrate their commitment through consistent actions, safety becomes embedded in the organizational DNA.
Leaders should regularly walk the floor to observe safety practices, provide feedback, and engage directly with staff about concerns. Safety performance must be part of management evaluations and recognized during employee reviews. Setting clear expectations, promptly addressing hazards, and allocating budget for training and equipment demonstrate leadership accountability.
Involving employees in safety committees or feedback sessions also fosters a sense of ownership. A visible and engaged leadership team reinforces that safety is not just a policy but a shared responsibility that starts at the top.
Employee Engagement and Participation
Engaging employees in safety initiatives is key to building a strong safety culture. Here are some effective methods:
- Safety Committees: Form committees with representatives from different departments to discuss safety concerns and propose improvements.
- Hazard Reporting Systems: Implement easy-to-use systems for employees to report potential hazards or near-misses without fear of reprisal.
- Safety Suggestions Program: Encourage employees to submit ideas for improving workplace safety and provide incentives for implemented suggestions.
- Peer-to-Peer Observations: Train employees to conduct informal safety observations of their colleagues, fostering a culture of mutual accountability.
- Safety Champions: Designate safety champions or ambassadors within each team to promote safety awareness and best practices among peers.
Safety Recognition and Incentive Programs
Recognizing and rewarding safe behaviors can significantly reinforce a safety-first culture. When employees see that their efforts to maintain a safe workplace are valued, they’re more likely to stay engaged and vigilant. Consider implementing:
- Monthly or quarterly safety awards for individuals or teams with outstanding safety records
- Milestone celebrations for achieving safety goals (e.g., 100 days without a lost-time incident)
- Points-based systems where employees earn rewards for completing safety training, reporting hazards, or participating in safety initiatives
- Public recognition via bulletin boards, newsletters, or SMS announcements
- Small but meaningful rewards such as gift cards, lunch with leadership, or extra break time
Consistent recognition creates friendly competition and shows that safety is a shared priority across the organization.
Effective Safety Communication Strategies
Clear and consistent communication is essential for maintaining a strong warehouse safety culture. Implement a multi-channel approach:
- Regular Safety Meetings: Hold brief, focused safety meetings at the start of each shift to discuss relevant hazards and reinforce important safety messages.
- Visual Communication: Use posters, digital displays, and floor markings to remind employees of safety protocols and highlight potential hazards.
- Two-Way Communication: Encourage open dialogue about safety concerns through suggestion boxes, safety hotlines, or digital feedback platforms.
- Mobile Communication Platforms: Use SMS-based employee communication tools to send real-time safety alerts, reminders, and updates. These platforms can also facilitate anonymous feedback and reporting, which can increase employee participation in safety programs.
How SMS-Based Communication Enhances Warehouse Safety
In warehouse environments, implementing effective communication strategies is necessary for maintaining safety standards and preventing accidents. SMS communication tools like Yourco have emerged as a valuable resource in warehouse safety communication, offering real-time alerts, increased accessibility, and improved engagement.
Real-Time Warehouse Safety Alerts and Updates
One of the most significant advantages of SMS-based communication is the ability to instantly notify staff of new hazards, weather-related risks, operational changes, or ongoing emergencies. This is made possible through an efficient employee notification system, ensuring timely distribution of important information.
This speed of communication can be life-saving in important situations. For example, during a chemical leak, an SMS alert can quickly direct workers to safe zones and communicate cleanup protocols, which is far more efficient than traditional methods like intercoms or emails.
The effectiveness of SMS communication is backed by impressive statistics. SMS messages have a 98% read rate compared to just 20% for emails, with an average response time of only 90 seconds. This high engagement rate ensures that important warehouse safety information reaches employees quickly and reliably.
Two-Way Communication for Hazard Reporting
Advanced SMS-based platforms like Yourco enable two-way communication, allowing employees to immediately report hazards, unsafe conditions, or near-misses. This real-time feedback loop triggers timely interventions and helps prevent potential accidents before they occur. Yourco also offers anonymous reporting options, encouraging workers to voice concerns without fear of reprisal.
Documentation and Compliance Benefits
SMS-based communication platforms provide a reliable digital record of all safety communications, ensuring companies can track and demonstrate compliance with OSHA regulations and internal safety audits.
These systems automatically log when safety information was sent, who received it, and who acknowledged it, offering transparency in communication. Automated text messaging can also be used to send reminders for safety checks, training deadlines, and policy updates, ensuring that safety procedures are consistently followed.
This level of documentation not only supports regulatory compliance but also helps reduce the risk of fines or penalties. With real-time updates and verifiable logs, SMS platforms like Yourco create an efficient way to maintain accountability and streamline compliance processes in warehouses.
To enhance documentation and compliance, it also captures and analyzes critical safety data to help HR and warehouse leaders proactively manage risks. With Yourco’s platform, every message is automatically:
- Tagged by type (e.g., “blocked fire exit,” “forklift issue”)
- Assigned to specific locations, shifts, and teams
- Flagged by repeat issue or severity level
This built-in Frontline Analytics layer surfaces essential trends that traditional communication methods miss. For example, it identifies locations with low reporting volumes, which may signal under-reporting or a weak safety culture. It highlights sites with frequent, unresolved safety alerts that demand immediate attention. It also uncovers patterns of specific incidents — such as repeated PPE violations or forklift accidents — that point to training gaps or operational shortcomings.
Yourco’s centralized dashboard provides HR and operations leaders with actionable insights. Leaders can quickly spot top and bottom-performing warehouses based on safety communication volume and resolution rates. It also flags sites that consistently fail to inform frontline workers in a timely manner about hazards, helping organizations intervene before small issues escalate. By analyzing trends over time, Yourco reveals where procedural improvements or additional training initiatives are needed.
By leveraging these analytics, warehouses can move from reactive safety management to proactive prevention. Identifying emerging risks early enables organizations to improve compliance, reduce incidents, and strengthen their overall safety culture
Overcoming Language Barriers
In diverse warehouse environments, language barriers can lead to miscommunication, increasing the risk of accidents and injuries. To address this, SMS-based communication tools like Yourco include multilingual messaging features, ensuring that workers from various language backgrounds receive clear, actionable safety instructions.
These platforms allow real-time alerts, hazard reports, and safety reminders in multiple languages, reducing confusion and enhancing worker understanding. Implementing such emergency alert systems is essential for overcoming language barriers, promoting workplace inclusivity, and ensuring that all employees can respond appropriately in critical situations.
By ensuring that safety information is accessible to everyone, companies can foster a cohesive safety culture, improve compliance, and protect the wellbeing of all workers, regardless of language proficiency.
Integration with Traditional Safety Methods
While SMS communication is powerful, it's most effective when integrated with traditional safety methods. For example:
- Use SMS to reinforce learning from in-person safety meetings with follow-up recaps and reminders.
- Combine clear physical signage in the warehouse with digital reminders through the employee communication platform for layered communication.
- Deliver micro-learning modules directly to mobile devices for just-in-time instruction, supplementing formal training sessions.
Using the immediacy and accessibility of mobile-first communication solutions alongside established safety practices creates a more robust and responsive safety ecosystem.
When executed effectively, these systems have proven to significantly enhance warehouse safety awareness, reduce accident rates, and foster a proactive safety culture in warehouse environments.
Monitoring and Evaluation of Warehouse Safety Practices
Ongoing monitoring and evaluation are necessary to ensure that safety measures in warehouses remain effective and continuously improve. Implementing a robust system of metrics, audits, and analysis helps warehouses identify trends, address emerging risks, and enhance their overall safety performance.
Key Warehouse Safety Performance Metrics
To effectively track safety progress, warehouses should focus on several important performance indicators:
- Total Recordable Incident Rate (TRIR): This metric measures the number of recordable injuries and illnesses per 100 full-time employees within a given time frame.
- Lost Time Incident Rate (LTIR): LTIR calculates the number of incidents resulting in lost work time per 100 full-time employees.
- Near-miss Reporting Rate: Tracking near-misses is necessary for proactive risk management.
- Safety Inspection Findings: This metric tracks the number and type of hazards identified during safety inspections.
- Safety Training Completion Rate: Monitoring the percentage of staff who have completed mandatory safety training ensures workforce competency.
Conducting Effective Safety Audits
Regular safety audits are essential for verifying compliance and evaluating the effectiveness of warehouse safety measures. These audits help identify potential hazards, prevent accidents, and ensure that safety protocols are consistently followed.
Key components of an effective safety audit include:
- Physical Inspections: Regularly check for hazards such as blocked exits, poorly maintained equipment, or damaged safety gear.
- Documentation Review: Examine safety records, training logs, and incident reports to ensure proper documentation and compliance with regulations.
- Employee Interviews: Engage with workers to gather insights on safety practices and identify areas for improvement.
- Process Evaluation: Assess the effectiveness of existing safety procedures and make adjustments as needed to address any gaps.
Analyzing Incidents and Near-Misses
A thorough analysis of incidents and near-misses is necessary for preventing future accidents and improving safety protocols. This process should include:
- Incident Investigation: Analyze every reported incident to uncover root causes.
- Root Cause Analysis: Identify the underlying factors that contributed to the incident.
- Corrective Action Tracking: Implement and monitor corrective actions based on investigation findings.
- Follow-up Reviews: Conduct follow-up assessments to verify the effectiveness of implemented measures.
Continuous improvement in warehouse safety relies on a comprehensive approach to monitoring and evaluation. Consistently collecting and analyzing safety data, engaging employees in the process, and adapting based on findings helps warehouses create a safer work environment, reduce accidents, and improve overall operational efficiency.
Warehouse Safety Excellence: Your Path to Success
Warehouse safety needs a multifaceted approach combining training, hazard awareness, protective equipment, clear communication, and supportive culture. Beyond compliance, this approach enhances operations and employee wellbeing. SMS-based communication tools offer game-changing advantages for reducing accidents through immediate alerts and updates.
Effective safety measures require regular training, hazard communication, proper PPE, clear emergency procedures, real-time communication, employee involvement, and regular evaluation. Yourco's SMS platform connects non-desk warehouse workers through their phones with 98% read rates and 90-second response times.
This system distributes safety alerts, enables hazard reporting, supports compliance documentation, and overcomes language barriers while integrating with existing procedures. Prioritizing safety with enhanced communication helps warehouses meet regulations, increase productivity, improve morale, reduce accident costs, and protect their most valuable asset—their people.
Try Yourco for free today or schedule a demo and see the difference the right workplace communication solution can make in your company.