How to Combine Six Sigma and Lean Manufacturing for Maximum Efficiency

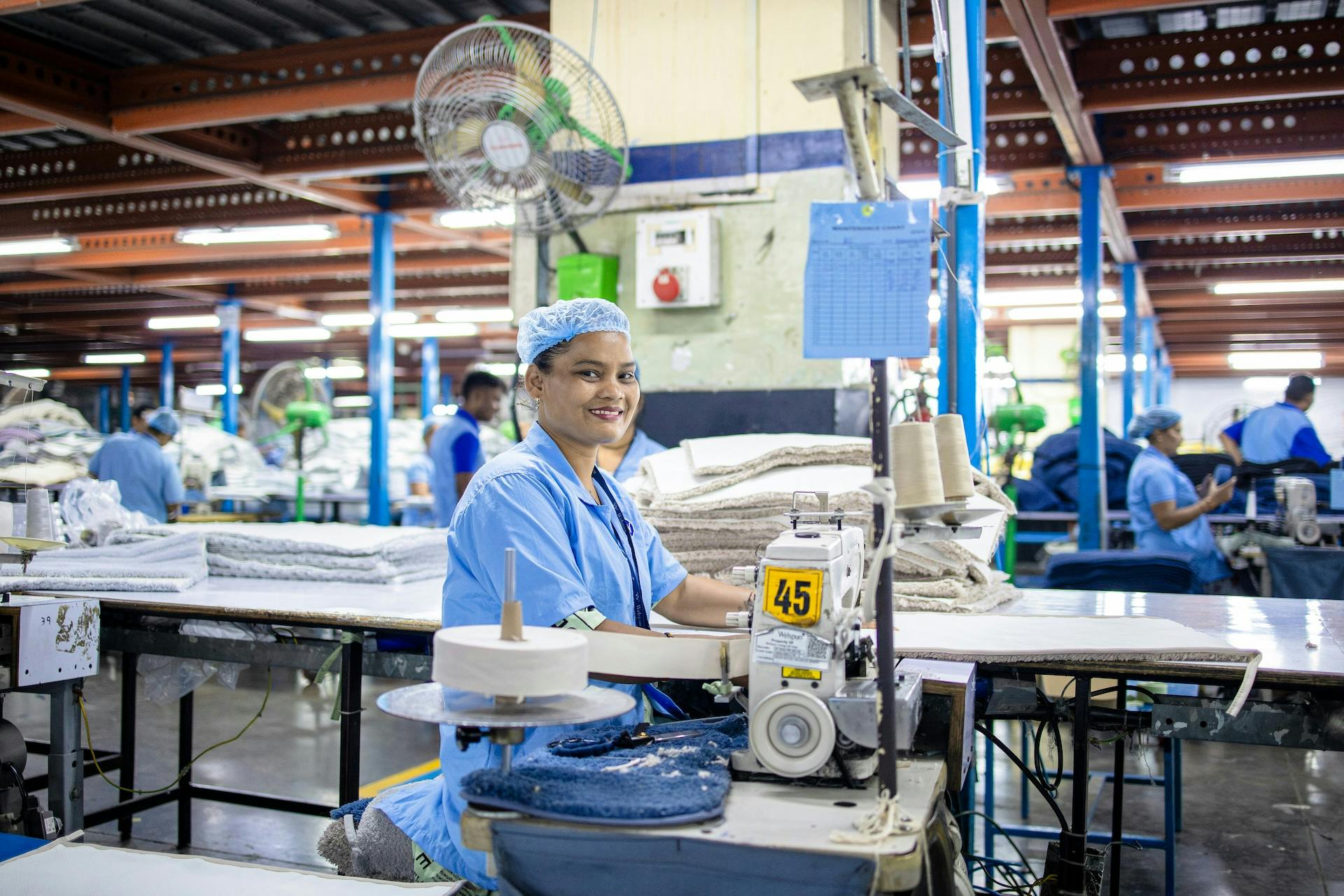
Operational efficiency separates thriving manufacturers from those struggling to keep up. When defects slip through your production line or materials sit unused, costs pile up fast, and customer trust erodes even faster. Many manufacturers tackle these challenges with two proven approaches: Six Sigma and Lean Manufacturing.
Each method delivers solid results on its own. Six Sigma ensures consistent quality and fewer mistakes, while Lean speeds up processes and cuts waste. But here's where it gets interesting — combining them into Lean Six Sigma creates something more powerful than either approach alone.
This integrated framework gives you the best of both worlds: Lean's quick wins paired with Six Sigma's analytical depth. The results are shorter lead times, leaner inventories, steadier quality, and fewer costly reworks. For multi-locational manufacturers, the benefits multiply. Shared metrics and common improvement tools create consistency across locations, making it easier to replicate successes and maintain momentum company-wide.
What is Six Sigma?
Six Sigma is a disciplined, data-driven approach that eliminates defects from any process until it delivers near-perfect results (3.4 defects per million opportunities or fewer). Motorola developed this method in the 1980s, and it has since become a global standard for quality improvement across industries.
Six core principles guide every project:
- Customer focus: Because value is defined by the people buying the product.
- Data-driven decisions: Every decision is based on hard data rather than gut feelings.
- Process focus: Because flawed processes create most problems, zero in on mapping, measuring, and refining them.
- Proactive management: Catching failure points before they hit production.
- Collaboration across functions: Collecting insights from operators, engineers, and managers.
- Continuous Improvement: Pushing toward perfection, always looking for that next improvement in consistency or capability.
These principles are put into action through the DMAIC cycle:
- Define the problem
- Measure current performance
- Analyze data to pinpoint root causes
- Improve the process with targeted fixes
- Control the gains so they stick
Each stage uses clear deliverables, such as process maps, statistical tests, and control charts, to keep you on track.
When you apply this methodology, you trim rework, scrap, and warranty claims. The result is consistent process performance, smoother production schedules, and happier customers. This translates directly into lower costs and higher throughput without adding headcount.
What is Lean Manufacturing?
Lean Manufacturing is a practical way to run your production floor so every action adds value and nothing else sneaks in. By zeroing in on waste, such as extra motion, waiting, and overproduction, you free up time, material, and cash that customers never agreed to pay for. The concept grew out of the Toyota Production System and has since spread well beyond automotive plants into nearly every industry imaginable, thanks to its clear, disciplined focus on value creation.
Most approaches center on five principles that work together to streamline operations:
- Define value from the customer's perspective: Consider what the customer truly cares about, such as price, features, delivery speed, and reliability.
- Map the value stream: Visualize every step from raw material to finished product, identifying activities that don’t add value.
- Create flow: Rearrange work so that materials and information move smoothly, without delays or bottlenecks.
- Establish pull: Produce only in response to actual customer demand, which reduces excess inventory and improves agility.
- Pursue continuous improvement: Make ongoing, incremental changes that refine processes over time and sustain long-term gains.
Many plants expand on those basics with additional practices such as respect for people, process standardization, visual management, and error-proofing. These ideas round out a culture where everyone can spot trouble early and fix it fast.
When you remove tasks that don't add value and smooth the flow, lead times shrink, quality problems surface sooner, and your operation can pivot quickly when demand shifts. The end result is a more agile factory that meets customer needs with less effort and lower cost.
Key Differences Between Six Sigma and Lean
If you picture these methodologies as two specialists on the factory floor, Lean is the efficiency expert rooting out anything that slows you down, while Six Sigma is the quality guru hunting every source of variation. Understanding what sets them apart helps you decide which one to call on first, or why using both often works best.
Lean Focuses on Speed and Flow
Lean centers on flow and speed. Its core question is simple: "Does this step add value for the customer?" Anything that doesn't, such as extra motion, waiting, and overproduction, counts as muda, or waste, and must go. By mapping the value stream and reorganizing workstations, teams regularly shave hours, even days, from lead times.
Six Sigma Prioritizes Consistency and Control
Six Sigma emerged decades later with a different obsession: consistency. Armed with statistical tools and the DMAIC roadmap, practitioners measure, analyze, and control processes until defects fall below 3.4 per million opportunities. The belt-based training system (Yellow, Green, Black, and Master Black) formalizes that expertise through structured certification levels.
Different Tools and Techniques
Because their goals diverge, their day-to-day methods do too. Lean favors continuous, team-driven tweaks such as 5S housekeeping, Kanban pull signals, and quick Kaizen events that deliver visible gains right away. Six Sigma tackles defined projects, often months long, that dig deep into root causes with control charts, hypothesis testing, and FMEA. Lean relies heavily on observation, while Six Sigma leans on data.
Visible Waste vs Hidden Variability
Focus areas also differ significantly. Lean attacks bottlenecks and inventory piles you can see; Six Sigma zeros in on hidden variability you usually detect only through numbers. When your assembly line suffers from parts shuttling back and forth, a sprint to rearrange stations and introduce single-piece flow provides fast relief. If customers complain about sporadic electronic failures, a DMAIC project can pinpoint solder-temperature variation and lock in tighter controls.
Cultural Adoption vs Specialist Expertise
Certification further separates the two approaches. Lean improvement often spreads through broad culture change where everyone learns to spot waste. Six Sigma's belt hierarchy assigns complex statistical work to certified specialists who mentor the wider team.
It’s worth noting that these distinctions are strengths, not conflicts. Lean gives you speed, while Six Sigma guarantees precision. Combining them lets you streamline flow and stabilize quality in one coordinated effort, putting both experts to work on the same problem and driving far bigger gains than either could deliver alone.
How Lean and Six Sigma Complement Each Other
When you bring these methodologies together, you get processes that move quickly and stay on target. Lean's focus on flow gives you immediate, visible wins, such as shorter lead times, smaller batch sizes, and less inventory. Six Sigma adds the statistical discipline that keeps those faster processes from drifting out of spec. The result is a single system that delivers both speed and precision simultaneously.
This approach also fills the gaps each method leaves behind. Lean can stall when a problem demands deeper data analysis. Six Sigma projects sometimes drag because teams are busy gathering numbers instead of fixing obvious waste. By blending the two, you let Lean's kaizen events kick-start change while Six Sigma's DMAIC cycle confirms root causes and secures controls.
A unified approach embeds Lean tools (5S, value stream mapping, and Kanban) inside each DMAIC phase. This creates a rhythm of quick action followed by rigorous validation. That structure is why companies adopting this integrated methodology often report significant gains in both productivity and quality, such as the 20 percent productivity lift achieved by an automotive plant in North West England after one year of integration efforts.
You also gain flexibility across multiple sites. The combined approach sets common metrics, such as defects per million, takt time, and first-pass yield, so that every plant speaks the same language. Yet individual teams are free to pick the mix of tools that fits their local constraints. A warehouse may rely on Kanban to control inventory pulls, while an assembly line runs a statistical process control chart to monitor torque variation. Because the methodology is built around clear roles (such as Champions, Black Belts, and front-line problem solvers), knowledge travels easily between locations. This helps you replicate success without having to start from scratch.
Most importantly, an integrated system reinforces a culture of continuous improvement. Lean reminds everyone to chase waste daily. Six Sigma teaches them to prove a fix works before celebrating. When employees see both philosophies working in tandem, they trust the data, rally around shared goals, and keep pushing for perfection. That cultural shift, more than any single tool, is what turns isolated improvements into sustainable, company-wide gains.
Common Tools Used in Lean and Six Sigma
Several tools work across both methodologies. Value stream maps evolve into detailed process maps during Six Sigma projects. 5S often becomes part of the "Improve" phase of DMAIC, locking in cleanliness standards that keep new process settings stable. Control charts provide the continuous feedback every Kaizen circle needs to verify that yesterday's improvement still works today
The key is matching the tool to the problem:
- For visible waste: Use Lean methods like Kanban or 5S.
- For Inconsistent results: Lean on data with DMAIC and control charts.
Most problems blend both — a pileup of inventory and a mysterious defect — so pairing a quick Lean fix with Six Sigma validation often delivers the fastest and most reliable gains. You don’t need every tool on every project. Start with the issue in front of you, choose the best-fit method, and let the results guide your next move.
How to Implement Lean Six Sigma
You launch this integrated methodology the same way you build any great product — by starting with a clear goal, assembling the right team, and proving value fast. When these three elements line up, the approach can cut production cycle time by as much as 70 percent and trim manufacturing costs by 50 percent.
1. Tie Projects to Business Priorities
Begin by tying every improvement effort to a business priority. Ask yourself what matters most right now. Is it faster lead times, fewer defects, a lower cost per unit, and whether each change will also keep you ahead of industrial regulatory compliance? Put numbers next to each objective, then secure an executive sponsor who can remove roadblocks and keep resources flowing.
2. Build a Belt-Based Team Structure
Next, build a team structure that matches your goals. A Champion vets project ideas and aligns them with strategy. Master Black Belts mentor full-time Black Belts, who coach part-time Green Belts and Yellow Belts embedded in the workforce.
This belt system clarifies ownership and creates an internal pipeline of problem solvers. When your operation spans multiple sites, designate at least one belt holder per location so local needs never get lost.
3. Deliver Hands-On, Role-Specific Training
Training cannot be a one-off slide deck. Provide role-specific courses that blend tools like 5S and Value Stream Mapping with statistical techniques. Practical exercises on your own lines speed up learning and show employees that the methodology fixes real headaches, not theoretical ones.
4. Launch with a High-Impact Pilot Project
With skills in place, choose a pilot project where success will be clear: a bottleneck line, a high-defect welding cell, or an assembly area drowning in rework. Map the current process, collect baseline data, and run through DMAIC. Remove obvious waste during "Measure," streamline flow in "Improve," and document new standard work in "Control." A well-executed pilot delivers quick wins that you can showcase to build momentum.
5. Keep Communication Clear and Consistent
Communication holds multiple sites and cross-functional teams together. Mobile employee communication apps keep Black Belts, operators, and supervisors in sync, speeding up feedback loops during each DMAIC phase.
Share progress dashboards daily, celebrate milestones, and keep language plain so anyone on the shop floor can understand why changes are happening. Frequent updates prevent rumors and reinforce the idea that this approach is a team sport, not a management fad.
6. Address Resistance and Data Challenges Early
Expect hurdles. Cultural resistance sets in when employees perceive the program as a cost-cutting exercise rather than a quality-of-worklife improvement. Counter it by involving operators in root-cause discussions and recognizing their contributions publicly.
Data quality issues also surface. Invest early in reliable measurement systems so analyses lead to the right fixes. Guard against backsliding by scheduling regular audits and tying process owners' performance reviews to the new standards.
7. Scale What Works and Standardize the Playbook
When the pilot sustains its gains for a few months, replicate the playbook on adjacent lines, then expand site-to-site. Standardize templates for charters, dashboards, and control plans so every new project starts faster than the last. Over time, you'll see the compound effect: smoother flow, near-zero defects, and a workforce that knows how to solve its own problems.
With the right structure, communication, and mindset, Lean Six Sigma becomes part of how your operation runs every day. Start small, prove value, and scale with intention to drive results that last.
Build a Lean, Reliable Operation With the Right Tools in Place
Combining these complementary methodologies in manufacturing operations maximizes efficiency and quality. When speed and precision work together, you create processes that are both fast and reliable. This integration reduces waste, minimizes defects, and improves flow, delivering consistent high-quality results. Starting small with pilot projects allows for scalability and helps build confidence in the approach before broader implementation.
A critical success factor in implementing these improvements is effective communication. Tools like Yourco ensure efficient communication across teams, especially for non-desk workers. Yourco's SMS-based platform supports continuous improvement initiatives by providing real-time updates, feedback collection, and cross-site coordination, making it easier to manage operations seamlessly.
By leveraging Yourco, you can streamline communication and enhance engagement, leading to smoother operations and improved performance. To experience these benefits firsthand, try Yourco for free today or schedule a demo.
FAQs
How Long Does a Typical Six Sigma Pilot Take?
Most manufacturing pilots run three to six months, enough time to cycle through DMAIC, validate improvements, and prove they hold under normal production loads.
Do I Need Certified Black Belts to Start?
Certification helps, but it isn't mandatory. What you can't skip is structured training in both waste elimination and statistical problem-solving so teams share a common language.
What if My Data Collection Systems Are Weak?
Start with manual checksheets and simple gauges while you build more robust measurement systems. Accurate baseline data is better than perfect data collected too late.