Industrial Regulatory Compliance: A Practical Guide for Manufacturing Leaders

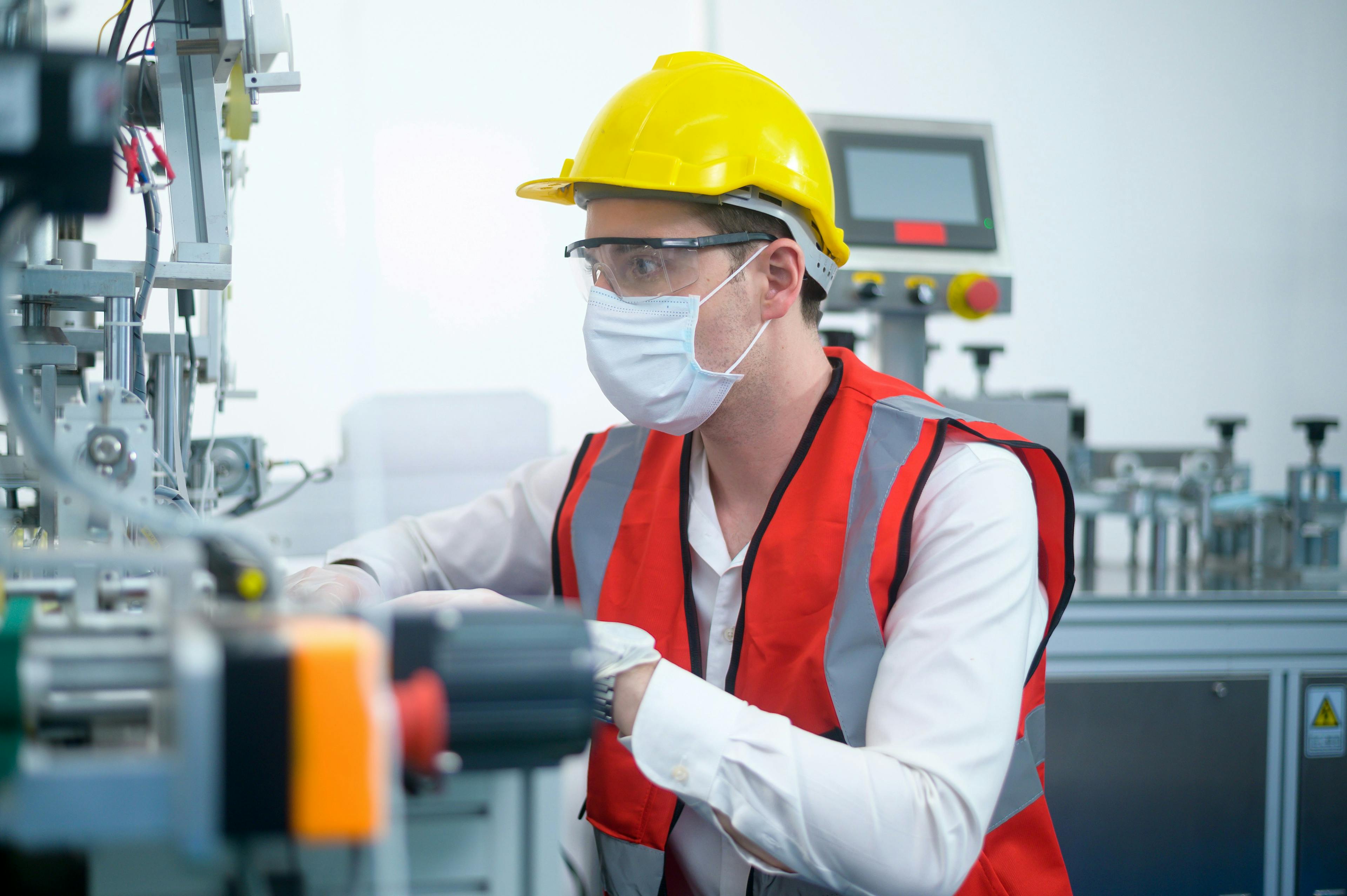
Industrial regulatory compliance can be challenging for those responsible for ensuring their organizations follow essential laws and standards. As regulations change frequently, staying current is crucial. This guide explores key strategies that manufacturers and others can use to maintain compliance, protecting their workers and reputation. By understanding compliance requirements and applying effective methods, companies can avoid legal penalties, improve efficiency, and create a safe workplace.
To comply, companies must follow guidelines from agencies like the Occupational Safety and Health Administration (OSHA) and the Environmental Protection Agency (EPA). These regulations protect workers, reduce environmental impacts, and uphold product standards. Compliance brings legal protection and improves reputation, which builds stakeholder trust and competitiveness. By making compliance part of their operations, companies meet legal and ethical standards, promoting responsibility and accountability.
Key Industrial Regulations and Standards
Understanding major regulations impacting industrial sectors is vital for compliance and efficiency.
The regulatory landscape manufacturers navigate today is more complex than ever. OSHA alone has hundreds of standards that could apply to your facility, from machine guarding requirements to chemical exposure limits. Add EPA regulations covering everything from air emissions to wastewater discharge, and you're looking at thousands of pages of requirements that change regularly.
What makes this particularly challenging is how these regulations interconnect. Your air quality permit from the EPA might trigger specific OSHA requirements for respiratory protection. A change in FDA guidelines for your product could necessitate updates to your quality management system under ISO 9001. This web of interconnected requirements is where many manufacturers struggle—not because they don't want to comply, but because tracking all these moving parts requires significant resources and expertise.
Standards & Agencies You Must Know
Multiple regulatory bodies oversee industrial operations, each with specific focus areas and enforcement powers. Understanding which agencies govern your operations helps you prioritize efforts and avoid costly violations that can halt production or result in hefty penalties.
OSHA (Occupational Safety and Health Administration) establishes workplace safety standards to protect employees from injuries and illnesses. Non-compliance can trigger work stoppages, fines reaching hundreds of thousands of dollars, and criminal liability for willful violations causing worker deaths. OSHA conducts unannounced inspections.
EPA (Environmental Protection Agency) controls emissions, waste disposal, and chemical handling. Emerging environmental regulations in 2025 include stricter refrigerant rules and enhanced air quality standards. EPA violations typically carry both civil and criminal penalties, with some reaching millions in fines.
DOT/FMCSA (Department of Transportation/Federal Motor Carrier Safety Administration) monitors transportation safety for companies moving goods or operating commercial vehicles. These agencies regulate driver qualifications, vehicle maintenance, and hazardous materials transport. Violations can cause authorities to revoke your DOT operating authority.
NFPA (National Fire Protection Association) and ISO 45001 provide fire safety codes and occupational health management standards. Local jurisdictions often adopt NFPA codes as law, while ISO 45001 demonstrates systematic safety management to regulators and customers.
SOX (Sarbanes-Oxley Act) requires publicly traded companies to maintain accurate financial reporting and internal controls. Manufacturing companies must document financial processes and maintain audit trails for all transactions. HIPAA affects industrial companies that handle employee health information or operate occupational health clinics. Data breaches can result in fines up to $1.5 million per incident.
PCI-DSS (Payment Card Industry Data Security Standard) governs any business that processes credit card payments, including employee cafeterias or customer transactions. NERC (North American Electric Reliability Corporation) oversees electric utilities and power generation facilities.
GDPR (General Data Protection Regulation) and REACH (Registration, Evaluation, Authorization, and Restriction of Chemicals) represent European regulations with global impact. GDPR affects any company handling EU citizen data, while REACH controls chemical imports and manufacturing.
The regulatory landscape evolves rapidly, with new AI safety requirements and environmental standards emerging regularly. Since regulations vary by location, operation type, and industry sector, you should conduct your own regulatory assessment to identify which specific requirements apply to your facilities.
Impact of Regulations on Manufacturing Operations
Compliance in manufacturing is legally required and strategically beneficial. It ensures worker safety, reduces accidents, and prevents expensive recalls. Compliance improves reputation, allows access to global markets, and builds consumer trust. Meeting ISO 9001 standards enhances product quality and efficiency, while following EPA regulations promotes environmental responsibility. Compliance contributes to a company's resilience and competitiveness. By integrating compliance, manufacturers handle regulatory challenges effectively, ensuring sustainable and ethical practices.
Challenges in Industrial Regulatory Compliance
Talk to any compliance manager over coffee, and they'll tell you the textbook challenges are just the beginning. Yes, regulations change frequently—but the real headache is figuring out which changes actually affect your specific operations. A single OSHA update might have implications for only certain types of machinery or processes, but determining that requires deep expertise and often expensive legal consultation.
Common Obstacles for Manufacturers
Manufacturers must constantly adapt to changing regulations, which can use up resources. Introducing new technologies for compliance, like automated monitoring systems, may cause compatibility problems with older systems. Keeping product quality high while ensuring supply chain compliance is a continual challenge. It's essential to streamline compliance without lowering standards.
Compliance Complexity Issues
Regulations are often complex, with different guidelines across regions and industries, which can overwhelm companies. Frequent changes require careful attention and proactive action. Compliance often needs substantial investment in staff and technology. Businesses operating in multiple areas with different requirements face an even greater compliance load. Frequent regulatory changes can cause stress among employees, requiring organizations to support employees during stress.
While compliance is vital for protection and advantage, overcoming challenges needs strategic planning and appropriate resource allocation.
Strategies for Effective Compliance Management
By integrating compliance management systems and emphasizing employee training and internal communication best practices, companies enhance adherence. This can be accomplished by developing a solid compliance strategy.
Implement Compliance Management Systems Thoughtfully
Modern compliance management systems can automate much of the documentation and tracking burden, but only if they're implemented thoughtfully. Choose systems that integrate with your existing operations rather than creating parallel workflows. Look for platforms that can send alerts directly to workers' phones—critical for reaching non-desk employees who might miss email updates.
Importance of Employee Training Programs
Technology is important, but people are essential. Ongoing training and effective communication strategies for safety protocols keep employees informed and compliant. Training helps them understand the importance of compliance and how to handle challenges. Strategies to engage non-desk workers are essential for effective training. Regular sessions promote a culture of compliance. Focusing on education allows quick adaptation to regulatory changes, maintaining safety and integrity.
By combining advanced systems with robust training andstrategies for effective employee communication, organizations manage compliance effectively, protecting against legal issues and promoting accountability and safety.
The 7-Step Industrial Regulatory Compliance Roadmap
Building effective compliance requires more than good intentions; it demands a systematic approach that transforms regulatory requirements into practical, sustainable operations. This proven 7-step roadmap draws from industry best practices and mirrors the DMAIC framework (Define, Measure, Analyze, Improve, Control) that manufacturing leaders already know. While we present these steps sequentially, you'll often work on multiple steps simultaneously as your program matures.
Step 1 – Identify Applicable Regulations & Scope
Your journey starts with understanding exactly which regulations apply to your specific operations. Industrial facilities often fall under multiple jurisdictions and regulatory bodies simultaneously.
Begin by conducting a comprehensive regulatory assessment through industry associations, legal counsel, and regulatory databases. Map each part of your operation against applicable regulations, considering factors like geographic location, product types, employee count, and environmental impact. A chemical manufacturing plant might answer to EPA environmental standards, OSHA workplace safety rules, DOT transportation requirements, and local fire codes all at once.
Prioritize regulations based on risk exposure, potential penalties, and operational impact. Some violations can shut down your facility immediately, while others carry financial penalties. Document your regulatory universe in a master registry that includes regulation names, applicable sections, deadlines, and responsible parties. This living document becomes your roadmap and helps prevent costly oversight.
Step 2 – Perform a Gap Analysis
With your regulatory landscape mapped, assess where you stand today versus where you need to be. Effective gap analysis starts with gathering accurate current-state data through facility audits, employee interviews, document reviews, and performance metrics. Don't rely solely on what managers think is happening, verify through direct observation and data collection.
Compare your current practices against each regulatory requirement, documenting specific gaps with quantifiable impacts where possible. If OSHA requires monthly safety inspections but you conduct them quarterly, calculate the gap and potential exposure. Use structured analysis tools like cause-and-effect diagrams to understand why gaps exist, whether from lack of resources, unclear procedures, inadequate training, or systemic issues.
Prioritize gaps based on risk, regulatory scrutiny, and implementation difficulty. Address immediate safety or environmental violations first, followed by gaps that could create significant penalties or operational disruptions. Set realistic timelines that consider your resources and constraints, but never compromise on critical safety or environmental issues that demand immediate attention.
Step 3 – Build a Cross-Functional Team
Compliance isn't a one-person job; it requires diverse expertise and organizational buy-in to succeed. Assemble a core team that includes a dedicated compliance officer with regulatory expertise, representatives from key departments (production, quality, environmental, safety), and an executive sponsor with authority to allocate resources and resolve conflicts.
Look for team members who combine technical knowledge with strong communication skills and change management experience. Your production representative should understand both floor operations and regulatory implications, while your quality representative needs to grasp both standards and practical implementation challenges. The executive sponsor must be someone who can remove barriers and ensure regulatory requirements remain a priority.
Establish clear roles, responsibilities, and communication protocols within your team. Effective programs require cooperation among production, quality assurance, legal, and environmental teams, so build regular touchpoints and decision-making processes that prevent silos. Your team should meet regularly to review progress, address emerging issues, and ensure activities align with operational priorities.
Step 4 – Develop Policies, SOPs & Documentation
Strong documentation forms the backbone of any industrial regulatory compliance program, providing clear guidance for employees and evidence for regulators. Start by creating comprehensive policies that establish your organization's commitment and outline roles, responsibilities, and consequences. These high-level documents set the tone and provide context for more detailed procedures.
Develop Standard Operating Procedures (SOPs) that translate regulatory requirements into specific, actionable steps your employees can follow. Effective SOPs include purpose statements, step-by-step instructions, decision points, safety considerations, and documentation requirements. Make them accessible and practical, because overly complex procedures that employees can't understand or follow consistently will create gaps rather than close them.
Establish documentation standards that ensure consistency across your operation, including naming conventions, revision control, approval processes, and storage systems. Your documentation should remain easily accessible to employees who need it while staying secure and audit-ready. Regular review and update cycles prevent procedures from becoming obsolete as regulations or operations change.
Step 5 – Train & Communicate with the Workforce
Even the best policies and procedures are worthless if your workforce doesn't understand or follow them. Develop training strategies tailored to different segments of your workforce—managers need broad oversight knowledge, while frontline workers need specific, job-relevant guidance. Use multiple delivery methods including classroom sessions, hands-on demonstrations, online modules, and peer mentoring to accommodate different learning styles and schedules.
Verify understanding through testing, demonstrations, and follow-up assessments rather than assuming attendance equals comprehension. Document all training activities meticulously, including participant lists, topics covered, assessment results, and remedial actions taken. This documentation proves your efforts during audits and helps identify knowledge gaps that need additional attention.
SMS-based communication platforms like Yourco ensure critical information reaches all workers regardless of their access to email or internet connectivity. Unlike traditional communication methods that non-desk employees often miss, SMS achieves read rates over 90% and works on any mobile device. All communications are logged and searchable for audits, creating the documentation trail regulators expect while ensuring no worker misses crucial safety alerts, policy updates, or training reminders.
Step 6 – Implement Controls, Record-Keeping & Incident Reporting
Effective compliance requires layered controls that prevent, detect, and correct non-conformance before it becomes a regulatory violation. Implement preventive controls like equipment maintenance schedules, safety checklists, and approval workflows that stop problems before they occur. Add detective controls such as monitoring systems, inspection programs, and performance reviews that catch issues early. Finally, establish corrective controls including incident response procedures, root cause analysis, and remedial action plans.
Establish robust record-keeping systems that capture activities in real-time rather than recreating them later for audits. Digital logs replace paper-based records and provide time-stamped documentation that's easily searchable and audit-ready. Your records should demonstrate not just activities but also their effectiveness and any corrective actions taken.
Create streamlined incident reporting and investigation procedures that encourage prompt reporting without fear of retribution. The faster you know about potential issues, the more options you have for resolution. Implement root cause analysis methodologies that go beyond immediate causes to identify systemic issues that could create future problems.
Step 7 – Monitor, Audit & Continually Improve
Sustained industrial regulatory compliance requires ongoing vigilance and continuous improvement rather than periodic efforts. Establish internal audit schedules that provide regular, systematic reviews of your program's effectiveness. Use risk-based approaches to determine audit frequency and scope—high-risk areas or those with previous issues need more frequent attention than stable, low-risk processes.
Track metrics and KPIs that provide early warning of potential problems, such as training completion rates, incident frequencies, audit findings, and corrective action closure times. Establish dashboards and real-time monitoring that give management visibility into status and trends rather than waiting for formal reports that may identify problems too late for effective response.
Implement management review processes that regularly evaluate your program's adequacy and effectiveness, making adjustments based on regulatory changes, operational modifications, or lessons learned from audits and incidents. Use continuous improvement methodologies to strengthen your program systematically, treating each audit finding or near-miss as an opportunity to enhance your overall posture.
Role of Technology in Compliance
Forget the marketing about "revolutionary compliance solutions." In real manufacturing environments, the technology that works is often surprisingly simple. SMS-based alert systems outperform sophisticated apps because they reach workers instantly without requiring downloads or logins. Basic automated monitoring beats complex AI systems when it reliably catches permit violations before they become citations. It’s always better to stay simple and immediate, reaching workers where they are.
Technology Facilitating Regulatory Compliance
Compliance management software changes how regulations are handled. These systems automate documentation, simplify processes, and provide real-time updates, reducing manual work. Platforms like SMS-based employee notification systems, which send SMS text alerts to non-desk workers, keep records for audits and reports. Technology also helps train employees who are not at desks, supporting compliance throughout organizations. The importance of IT in manufacturing training cannot be overstated.
Contribution of Automated Monitoring Systems
Automated systems support compliance by tracking adherence and alerting to violations. Data analytics predict risks, allowing proactive actions. AI tools manage compliance data, ensuring regulatory alignment. Using AI reduces non-compliance risks, enhancing transparency and accountability. Implementing AI requires attention to data protection and ethical use, which technology can help manage.
Using technology tools enables efficient compliance management, reduces risks, and lets companies focus on their main activities, maintaining competitiveness.
As manufacturers adopt AI and machine learning tools for predictive maintenance and quality control, new compliance considerations emerge. These systems often process sensitive data, triggering privacy regulations. They make decisions that affect worker safety, creating liability questions. Smart manufacturers address these challenges upfront, building governance frameworks that ensure AI tools enhance rather than complicate compliance efforts. To do that, you need an AI compliance plan.
Implementing an AI Compliance Plan
Crafting a robust AI compliance plan is essential, ensuring adherence to regulations and preparedness for future landscapes.
Start by creating a governance framework with policies on AI use. Regular risk assessments identify issues early for timely action. Use AI tools to monitor compliance and automate violation detection. Strong data governance ensures alignment with regulations like GDPR. Regular audits evaluate strategy effectiveness and suggest improvements.Communicating openly with regulators can also help you to stay ahead of requirements. Engage proactively to understand trends and adjust strategies. Independent audits offer external compliance perspectives, providing insights and validation or you can integrate these tasks into your existing compliance team’s duties
This approach reduces risk and positions businesses as responsible industry participants. Though there are not yet universal standards for AI compliance, staying ahead will give you the best chance of preventing issues.
Ensuring a Compliant Future for Your Business
Ensuring your business is compliant isn't just about legal requirements; it's about creating a safer, more efficient, and trustworthy operation. By planning strategically, using technology, and investing in ongoing education, you can build a culture of compliance that benefits everyone.
Navigating these complexities doesn't have to be overwhelming. That's where Yourco comes in. As a leading SMS-based employee app designed for the non-desk workforce, Yourco bridges the communication gap between management and employees in manufacturing. With Yourco, you can send important compliance updates, training reminders, and safety alerts directly to your team's mobile phones, ensuring everyone stays informed wherever they are.
Yourco's straightforward and reliable platform makes it easy to manage your compliance communications effectively. By sending messages through SMS, you can reach your workforce instantly without requiring them to download apps or have constant internet access. This ensures critical information is received and acknowledged promptly, reducing the risk of non-compliance due to miscommunication.
Simplify compliance management with Yourco, and build a safer, more efficient workplace.Try Yourco for free today orschedule a demo and see the difference a dedicated communication solution can make in keeping your company compliant and your workforce connected.