Top 11 Challenges in the Logistics Industry and How to Solve Them in 2025

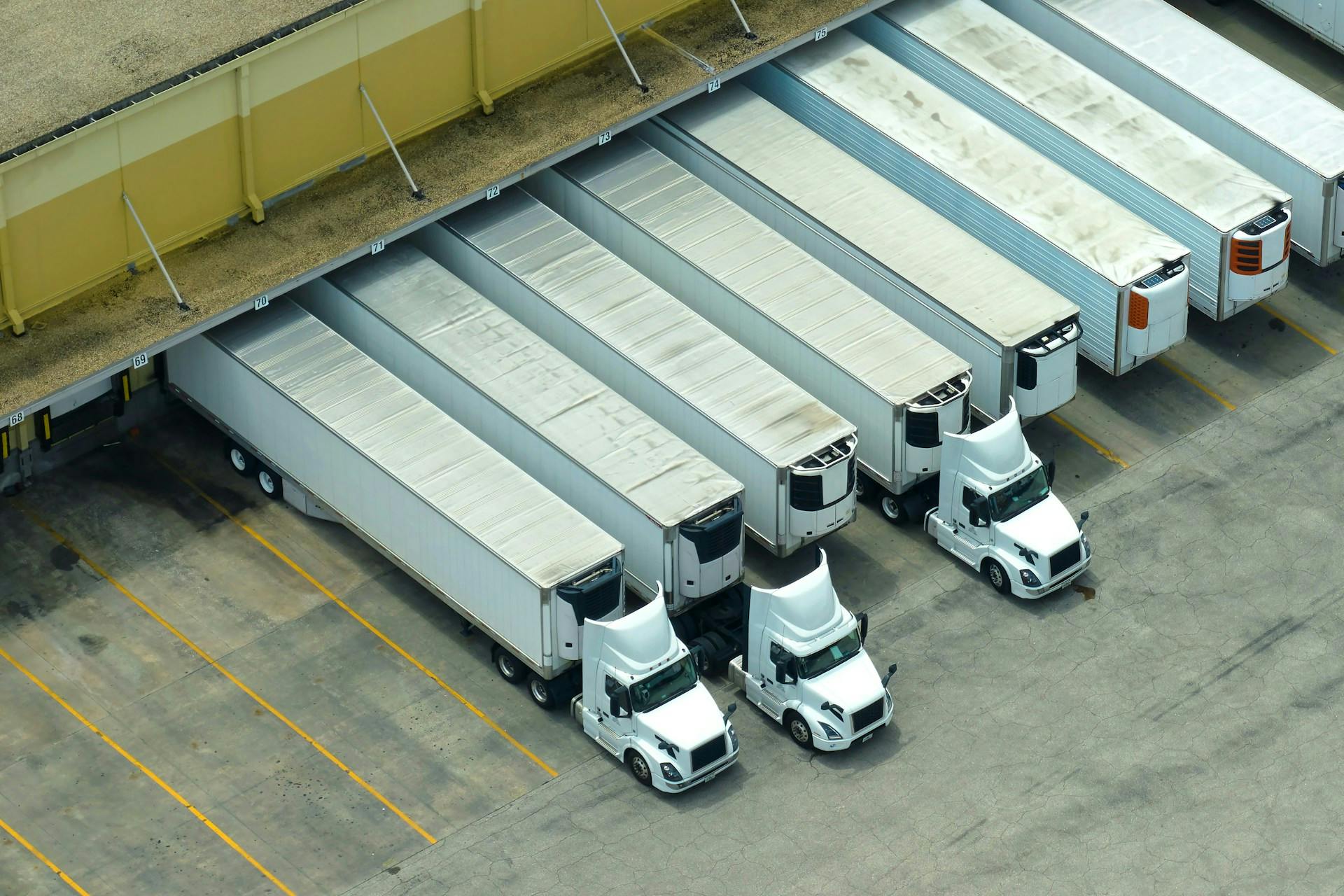
Global logistics is under immense pressure. Supply chains stretch across continents, while customers expect fast delivery and full transparency. Every late package, missing pallet, or stalled truck triggers ripple effects that increase costs and erode customer trust.
At the same time, logistics professionals are dealing with more and more complexity. Urban congestion, rising fuel prices, workforce shortages, and outdated systems are just a few of the issues testing even the most experienced teams. These aren’t isolated problems, they're deeply interconnected, and solving them requires smarter, more resilient operations.
This article explores the top 11 challenges facing the logistics industry in 2025 and the practical solutions companies are using to move faster, operate more efficiently, and stay competitive.
Challenges in the Logistics Industry
From rising costs to labor shortages and disconnected tech, the logistics sector faces a complex mix of operational, regulatory, and customer-driven pressures. Below, we break down the biggest challenges logistics leaders are facing in 2025 and the smart strategies that are helping them stay ahead.
1. Lack of Real-Time Tracking
Want to know where your stuff is? So does everyone else. End-to-end visibility means seeing your inventory and shipments in real-time, at every step. Without it, you're making decisions in the dark, wasting money and time.
The gap is still huge. Despite all our fancy tech, 43% of companies can't track items between handoff points, especially when crossing borders or switching from ships to trucks.
Smart companies are fighting back with cloud-based Transportation Management Systems and IoT sensors that create digital twins of their physical supply chains. These technologies enable continuous monitoring of conditions like temperature, humidity, and handling—critical for sensitive goods like pharmaceuticals and electronics.
The investment pays off quickly through reduced losses, better planning capabilities, and enhanced customer trust that comes from offering precise location updates throughout the journey.
2. External Disruptions
Supply chains break easily. Weather, politics, pandemics; they all throw wrenches in the works.
Remember the chip shortage? It showed how depending on single sources can freeze entire industries. The winners today are building diverse supplier networks and keeping strategic inventory buffers at key points, balancing efficiency with security.
The most resilient companies are developing sophisticated risk models that integrate real-time global events with supply chain vulnerability mapping. These predictive systems can recommend alternative routings, supplier shifts, or inventory adjustments before disruptions fully materialize. Modern resilience strategies also include regular simulation exercises to test response protocols and identify weaknesses before real crises hit.
3. Urban Congestion Problems
Cities are a delivery nightmare. Trucks sit an average of around 16 minutes in traffic per delivery in major metros, burning time and money while customers fume.
The fix? Mini-warehouses tucked into urban areas, combined with smart routing that adapts to traffic in real-time. Companies testing these approaches have cut delivery times in early trials.
Urban logistics challenges require multi-faceted solutions that account for infrastructure limitations, municipal regulations, and environmental concerns. Many pioneering companies are exploring:
- Off-peak delivery programs are negotiated with municipalities to allow nighttime operations when streets are clearer
- Micro-mobility solutions like cargo bikes and small electric vehicles for final-mile delivery in dense districts
- Collaborative drop points where multiple carriers share secure locker systems to consolidate delivery stops
This integrated approach recognizes that urban logistics requires collaboration between private companies, city planners, and property managers to create sustainable delivery ecosystems.
4. Rising Delivery Costs
The impossible equation: customers want packages yesterday, but fuel costs swing up to 40% year-over-year. The math doesn't work for many delivery companies.
Success stories come from those using zone-based pricing that reflects true costs while partnering with gig delivery services during rush periods. This mix keeps service quality high without breaking the bank.
Forward-thinking logistics providers are exploring innovative cost management techniques like dynamic route optimization that continuously recalculates the most efficient delivery sequences as new orders arrive. They're also investing in alternative-fuel vehicles and advanced analytics that identify hidden cost drivers across operations.
Another emerging approach involves collaborative shipping networks where competing companies share transportation capacity to reduce empty miles and improve overall utilization rates across the industry.
5. Escalating Customer Expectations
Modern consumers expect same-day or next-day delivery as standard service. Meeting these expectations while maintaining profitability creates enormous pressure on logistics operations. Companies struggle to balance speed with cost-effectiveness.
Innovative businesses are implementing local fulfillment centers and predictive analytics to anticipate demand patterns, placing inventory closer to end customers before orders even arrive. This pressure is compounded by the growing demand for delivery personalization, including precise time windows, special handling instructions, and real-time communication options.
Leading logistics providers are deploying sophisticated preference management systems that capture individual customer delivery profiles and automatically route shipments accordingly.
Some are even experimenting with subscription models that offer premium delivery options at a fixed monthly cost, creating predictable revenue streams while meeting heightened expectations.
6. Labor Shortages
Logistics has a people problem. With an average workforce age of 45 and warehouse turnover above 35% annually, companies bleed productivity and training dollars.
The smartest players have created mentoring programs spanning generations, implemented structured onboarding processes, and flexible schedules that match various lifestyle needs. Some are bringing back retired pros part-time to fill critical knowledge gaps.
The challenge extends beyond simply finding workers to finding the right workers with appropriate skills and retaining them in a competitive market. Industry leaders are addressing this through:
- Competitive compensation packages that include non-traditional benefits like emergency savings programs and education assistance
- Career advancement pathways are clearly mapped out for entry-level workers to see growth potential
- Workplace modernization initiatives that reduce physical strain and create more appealing environments
These comprehensive approaches, including enhancing frontline worker benefits, recognize that solving the labor crisis requires fundamentally rethinking the employment proposition in logistics.
7. Skill Gaps in the Workforce
As logistics technology advances, finding workers with appropriate technical skills becomes increasingly difficult. Traditional roles now require digital literacy and familiarity with sophisticated management systems.
Companies addressing this challenge implement targeted training programs and partnerships with educational institutions to develop talent pipelines specifically designed for modern logistics operations. The skills gap is particularly pronounced in specialized areas like predictive analytics, robotics maintenance, and systems integration.
Progressive logistics providers are creating internal academies that offer micro-credentials and continuous learning opportunities tailored to specific operational needs. They're also redesigning workflows to make complex systems more intuitive, employing visual interfaces and guided processes that reduce training requirements.
Some companies have also found success with "reverse mentoring" where younger, tech-savvy employees help experienced workers adapt to new systems.
8. Communication with Employees
Try reaching a driver during their route or a warehouse worker mid-shift. Unlike office staff, frontline logistics workers rarely check email while working.
Text messaging has become the go-to solution. These systems enable instant alerts about route changes or priority shipments as SMS is extremely effective when managing multi-location communication across diverse teams.
Two-way texting platforms also allow workers to report problems or updates immediately while giving managers quick polling tools to gather real insights from the field.
Companies focusing on SMS employee communication for non-desk workers report significant improvements in employee satisfaction and retention alongside operational performance gains.
9. Compliance Complexity
Shipping across borders means swimming through red tape. Customs forms, trade agreements, and country-specific paperwork create a maze that changes constantly and punishes mistakes severely.
One missing document can trap shipments at borders for days, with fines exceeding $10,000 per incident. Companies are turning to specialized software that automatically creates and checks documentation using constantly updated regulatory databases.
For businesses looking for effective regulatory compliance tips, adopting such software solutions can streamline operations and reduce risks.
The compliance challenge intensifies with growing sustainability regulations, carbon reporting requirements, and ethical sourcing documentation. Leading logistics providers are building robust compliance frameworks that:
- Centralize regulatory intelligence gathering across all operating regions
- Automate documentation creation with built-in validation and error-checking
- Create audit trails that prove due diligence in case of regulatory inquiries
- Provide continuous training for staff on emerging compliance requirements
This comprehensive approach transforms compliance from a cost center into a competitive advantage that enables smooth border crossings and faster customs clearance.
10. Green Logistics Requirements
Being eco-friendly isn't optional anymore. Most consumers check environmental practices before buying, while investors and governments demand carbon cuts.
Leading logistics companies are responding with electric vehicles, carbon tracking systems, and less packaging. Beyond satisfying external demands, these programs often save money through reduced fuel use and less waste.
The sustainability challenge extends beyond carbon emissions to encompass comprehensive environmental impact management.
Forward-thinking logistics providers are developing circular economy initiatives that recover and repurpose packaging materials, implementing water conservation programs at distribution centers, and integrating sustainability metrics into core performance dashboards. They're also collaborating with customers on joint initiatives like consolidated shipping programs that reduce total transportation needs across supply chains.
11. Technology Integration Challenges
Most logistics operations run on digital duct tape. Companies typically juggle 5-15 separate systems that don't talk to each other. Manual data transfers between old ERPs, warehouse systems, and transportation platforms create errors and delays.
Success stories come from companies using API-first platforms and flexible middleware that connects systems without requiring complete replacements. This allows step-by-step improvement rather than risky all-at-once overhauls.
The integration challenge is compounded by accelerating technology change and the need to incorporate emerging tools like artificial intelligence, autonomous vehicles, and blockchain validation systems.
Leading logistics providers are establishing technology governance frameworks that evaluate new solutions against standardized criteria and integration requirements. They're also creating cross-functional technology teams that bring together IT specialists with operational experts to ensure new systems address real business needs.
Driving Supply Chain Success with Effective Communication
Logistics in 2025 is defined by complexity, speed, and constant pressure to adapt. Solving the industry's biggest challenges—like real-time visibility, labor shortages, compliance, and rising customer expectations—requires more than isolated tools. It requires a system that keeps your workforce informed, responsive, and connected at every step.
Yourco is built for this reality. By using SMS, the most accessible and familiar communication method available, Yourco bridges the gap between operations teams and the non-desk workers who keep the supply chain moving. Drivers, warehouse staff, and dispatchers can send and receive messages instantly, without the need for apps, data plans, or training. This improves response times, minimizes errors, and enables better coordination across locations.
The platform doesn’t stop at messaging. With Yourco, drivers can text photo documentation as proof of delivery or to report damaged goods, giving managers time-stamped visual evidence in seconds. This helps reduce customer disputes, supports insurance claims, and protects your bottom line from costly chargebacks. It also strengthens accountability and builds trust with customers who now expect transparency at every touchpoint.
Yourco also simplifies compliance workflows by making it easy to distribute policy updates, confirm acknowledgments, and document communication trails—all over text. Combined with its secure architecture, audit-friendly logging, and native integrations with over 240 HRIS and payroll systems, Yourco becomes more than a communication tool. It becomes a strategic advantage.
In a world where every delay has a cost and every interaction matters, Yourco helps logistics teams stay ahead. Clearer communication means fewer mistakes, faster deliveries, and a more resilient operation from end to end.
Try Yourco for free today or schedule a demo and see the difference the right workplace communication solution can make in your company.