HR Guide to Field Hazard Assessments

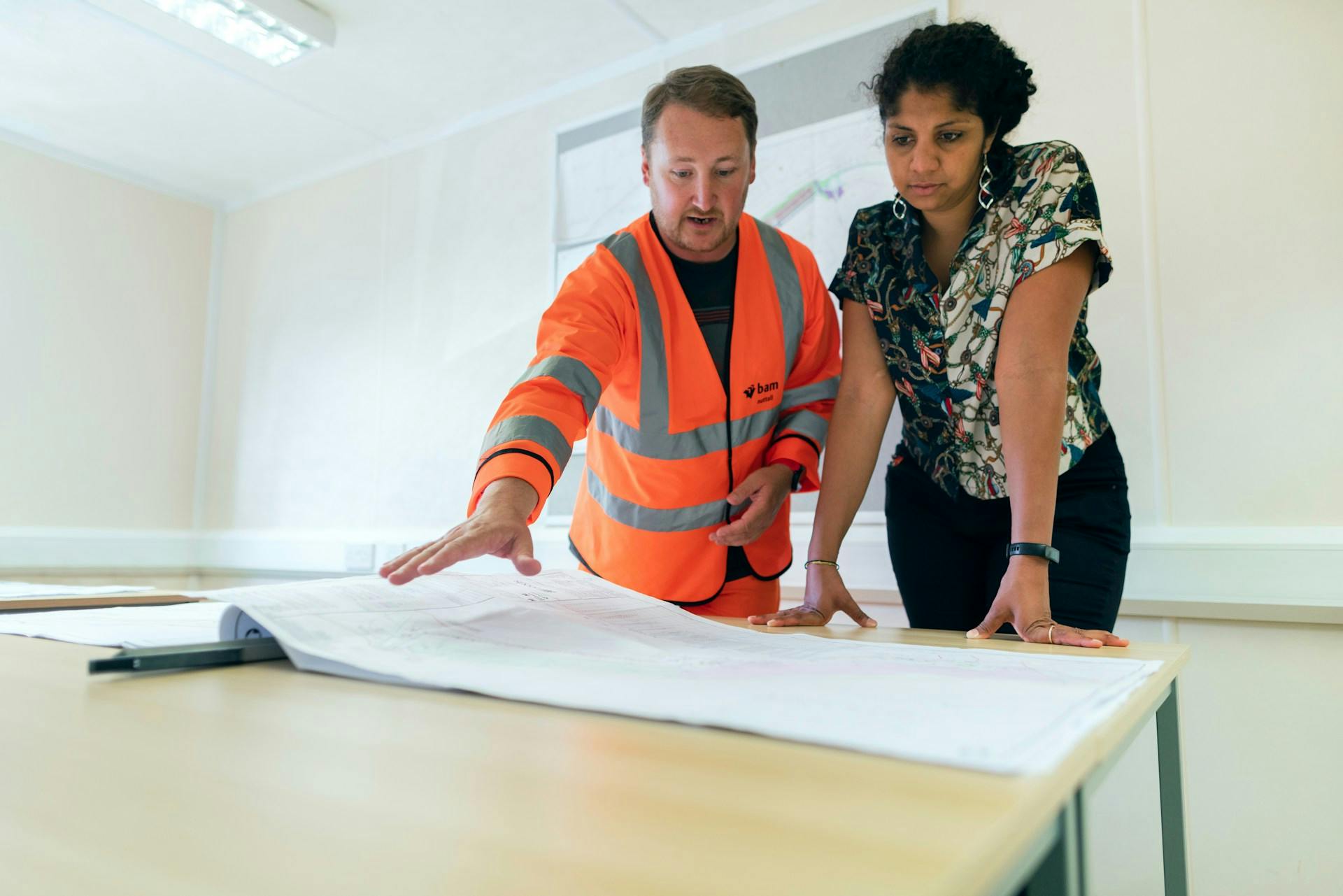
For workers who don’t sit behind a desk, such as those in construction, manufacturing, agriculture, mining, and oil and gas, the job site is where risk lives. These employees face hazards that shift throughout the day. They work around moving equipment, chemical exposure, extreme temperatures, and constantly changing environments. In these settings, a written safety plan alone is not enough.
HR managers and safety leaders need tools that match the pace and unpredictability of fieldwork. A Field Level Hazard Assessment (FLHA) provides that structure. It is a short, focused safety check performed before a task begins. This guide explains how to use FLHAs effectively to protect your workforce, meet compliance standards, and create a safer, more responsive workplace.
What is a Field Level Hazard Assessment?
A Field Level Hazard Assessment (FLHA) is a quick, on-site safety check completed just before work begins. It identifies hazards, evaluates risks, and puts control measures in place before tasks start. Unlike broader safety plans, FLHAs focus on real-time conditions at the exact location where work is happening.
This real-world approach helps catch hazards that may be missed during general planning. It also aligns with OSHA requirements for regular workplace inspections, incident investigations, and hazard reviews, even though FLHAs are not named explicitly in regulations. Construction sites, in particular, often require more frequent assessments due to their constantly changing nature, but industries like oil and gas, manufacturing, and healthcare benefit as well.
The value of FLHAs extends beyond compliance. They prevent injuries, minimize downtime, and reduce both direct and indirect costs linked to workplace incidents. Consistent use also improves employee engagement, showing workers that their safety is a daily priority.
To get the most from each FLHA:
- Conduct them at shift start, after breaks, or when work conditions change
- Use standard forms or digital tools to ensure consistency
- Involve the workers doing the task as they know the risks best
- Link findings to broader safety systems and daily safety talks
- Provide training in hazard recognition and control strategies
When done right, FLHAs make safety proactive rather than reactive. They keep operations running smoothly and teams better protected.
Categories of Hazards in Field Level Hazard Assessment
Physical Hazards
These are often the most visible hazards in any workplace. They include:
- Equipment and machinery: Moving parts, pinch points, and unguarded machines that can crush, cut, or trap workers
- Electrical hazards: Exposed wiring, damaged cords, and poor grounding that can lead to shock or electrocution
- Fall hazards: Slippery surfaces, unguarded edges, ladders, and unstable structures
- Struck-by and caught-between: Risks from falling objects, moving vehicles, and heavy machinery
- Noise and vibration: Prolonged exposure can damage hearing and joints over time
- Temperature extremes: Both heat exhaustion and frostbite are serious concerns
- Weather-related risks: Rain, snow, wind, or lightning that can rapidly change worksite safety
Regular inspections should also look for:
- Missing machine guards
- Faulty lockout/tagout procedures
- Damaged tools or frayed wires
- Poor ergonomic conditions or unmarked danger zones
Chemical Hazards
Chemical risks are less visible but often more dangerous due to long-term effects. Common dangers include:
- Toxic substances: Harmful by inhalation, ingestion, or skin contact
- Corrosives: Acids and bases that can burn skin, eyes, and respiratory systems
- Flammables and explosives: Especially dangerous in confined spaces or near sparks
- Reactive chemicals: May cause violent reactions when exposed to heat, air, or water
- Carcinogens: Long-term exposure can lead to cancer
- Asphyxiants: Displace oxygen in confined areas, causing unconsciousness or death
Safe chemical handling requires:
- Access to Safety Data Sheets (SDS)
- Proper ventilation and storage protocols
- Emergency spill procedures and training
- Substituting hazardous chemicals with safer alternatives when possible
Biological Hazards
These involve organisms that can cause illness or infection. Examples include:
- Viruses, bacteria, and fungi: Spread through air, water, or contact
- Parasites: Transmitted via contaminated materials or hosts
- Bloodborne pathogens: Such as HIV and hepatitis, especially in healthcare
- Animal and insect-borne diseases: Like Lyme disease and rabies
- Mold and allergens: Common in damp or poorly ventilated buildings
Control strategies should include:
- Personal protective equipment (PPE)
- Handwashing stations and sharps containers
- Cleaning and disinfection protocols
- Vaccination programs and exposure control plans
Ergonomic Hazards
These hazards develop over time and often go unnoticed until the damage is done. Key concerns:
- Repetitive motions: Can cause tendonitis, carpal tunnel syndrome, and more
- Improper lifting: Leads to back injuries, herniated discs, or strains
- Poor posture and workstation design: Causes stress on joints and muscles
- Static positions: Prolonged standing or sitting without breaks reduces blood flow
- Heavy manual handling: Without lifting aids, it quickly overworks the body
Preventive steps include:
- Adjustable workstations and tool design
- Mechanical lifting assistance
- Job rotation and microbreaks
- Training on proper body mechanics
- Early detection and ergonomic assessments
Psychosocial Hazards
These affect mental health and can lead to physical consequences. Watch for:
- Work-related stress: Affects focus, increases mistakes, and raises injury risk
- Workplace violence: From verbal abuse to physical assault, common in customer-facing roles
- Harassment: Disrupts emotional safety and team dynamics
- Fatigue: Caused by long hours, lack of sleep, or poor scheduling
- Isolation: Working alone reduces emergency response and social support
- Job insecurity and poor communication: Amplify stress and reduce morale
To reduce these risks:
- Establish violence prevention programs
- Maintain reasonable schedules and allow rest
- Encourage regular manager check-ins with remote or isolated workers
- Provide Employee Assistance Programs and mental health resources
- Create open channels for feedback and incident reporting
The Field Level Hazard Assessment Process
Field Level Hazard Assessments (FLHAs) are the frontline of proactive safety. When done consistently, they prevent incidents by catching risks before a task begins. The FLHA process has four essential steps: identifying hazards, assessing risk, implementing controls, and reviewing outcomes.
Step 1: Identify Hazards
Hazard identification is the foundation of every FLHA. At this stage, the goal is to scan the worksite with fresh eyes and spot anything that could harm workers, damage equipment, or disrupt operations.
Begin by walking the job site and observing conditions as they exist—not as they’re written in policy. Look at tools, equipment, surfaces, lighting, and weather. Is anything missing, damaged, unstable, or misplaced? Don’t rely solely on visual cues. Listen for abnormal sounds, feel for extreme heat or vibration, and talk to the team about recent close calls or breakdowns.
Make it a point to observe workers doing their tasks. Procedures written on paper often diverge from what actually happens in the field. Watch how people move, what shortcuts they take, and how they interact with tools and each other.
To make hazard identification more effective:
- Include workers in the process—they’re the ones who understand the practical realities of the job.
- Review recent incident logs, near misses, and safety alerts from your organization.
- Use a checklist that covers the five major hazard types: physical, chemical, biological, ergonomic, and psychosocial.
Hazards don’t always announce themselves. Sometimes it takes multiple perspectives to see the whole picture.
Step 2: Risk Assessment
After hazards have been identified on the worksite, the next step is understanding the level of danger each one poses. Not all hazards are equally urgent, and without a structured assessment, it's easy to focus on the wrong risks. A strong risk assessment allows safety teams to prioritize responses, allocate resources efficiently, and ensure that the most serious threats are addressed before work begins.
Understanding Likelihood and Severity
The most common approach to assessing risk involves evaluating both the likelihood of a hazard occurring and the severity of its potential consequences. Likelihood refers to how often a particular hazard might realistically cause harm. Some events may be rare or tied to unusual circumstances, while others may occur frequently in day-to-day operations. Severity, on the other hand, describes the impact if that hazard does occur. A small cut requiring a bandage is not the same as a fall from a ladder that results in hospitalization.
These two factors—likelihood and severity—are typically plotted in a risk matrix, which visually categorizes risks from low to extreme. Hazards that are both highly likely and highly severe demand immediate action. In contrast, those that are unlikely and would cause only minor harm may be acceptable with ongoing monitoring.
Risk matrices are useful because they standardize judgment and help teams make consistent decisions, even across different job sites or departments. This method is especially helpful when field supervisors need to triage multiple hazards quickly and determine which to escalate first.
Applying Job Safety Analysis (JSA)
For tasks that involve multiple steps or carry complex risks, a Job Safety Analysis (JSA) offers a more structured and detailed method of risk assessment. Rather than assessing hazards in isolation, a JSA examines an entire task from start to finish, breaking it down into individual steps. For each step, the team identifies associated hazards and considers what could go wrong.
For example, if a job involves operating a mechanical press, the JSA would look at setup, loading materials, operating the machine, and cleanup. Each phase is reviewed for potential pinch points, energy release, repetitive strain, or equipment malfunction. Then, appropriate controls are determined for each hazard.
JSAs are particularly valuable for high-risk or technical operations, where a general FLHA might miss step-specific dangers. They also serve as excellent training tools, helping new workers understand both the tasks and the associated safety procedures.
Using Energy-Based Risk Assessment
In many workplaces—especially those involving heavy machinery, electrical systems, or industrial processes—hazards often stem from uncontrolled energy. An energy-based risk assessment identifies the types of energy present in a task and assesses how that energy could be unintentionally released.
This could involve mechanical energy from rotating equipment, electrical energy from exposed wires, hydraulic pressure in lifting systems, or chemical energy in reactive substances. The assessment asks key questions: What happens if this energy escapes control? Who or what would be affected? Are there fail-safes or backup systems in place?
Understanding energy flow helps safety teams design better controls. For instance, a pressurized tank may appear stable until a valve fails. By accounting for stored energy and potential failure points, the team can install relief valves, physical barriers, or lockout/tagout procedures that neutralize the risk before it turns into an incident.
The purpose of any risk assessment is to inform what happens next. Once hazards have been evaluated using the appropriate method—or a combination of them—the findings are translated into action plans. Higher-risk items move to the top of the priority list for control implementation. Documentation at this stage is critical, not only for compliance, but to ensure continuity across shifts and teams.
Ultimately, risk assessment turns a raw list of hazards into a targeted roadmap for prevention. It brings clarity to uncertainty, giving supervisors and workers a shared understanding of which risks are most serious and how they should be addressed.
Step 3: Implement Control Measures
Now it’s time to act. Every identified risk should be matched with one or more control measures designed to eliminate or reduce harm. The best way to do this is by using the Hierarchy of Controls, which organizes controls from most effective to least:
- Elimination – Remove the hazard entirely
Example: Discontinue use of a faulty machine rather than repairing it temporarily. - Substitution – Replace the hazard with something safer
Example: Use a non-toxic cleaning agent instead of an industrial solvent. - Engineering controls – Physically separate workers from hazards
Example: Install guardrails, ventilation, or sound-dampening enclosures. - Administrative controls – Change how the work is performed
Example: Introduce rotating shifts for repetitive tasks or restrict access to high-risk areas. - Personal Protective Equipment (PPE) – Equip workers with protective gear
Example: Gloves, goggles, respirators, hard hats, and high-visibility clothing.
It's important not to skip steps in the hierarchy. PPE, for example, should be a last line of defense, not a first choice.
Involve workers when selecting and testing controls. Their insights help ensure that controls are both effective and realistic. Document all control measures, assign accountability, and provide training that’s specific to the task and the worker’s role. Reinforce what the control is, why it matters, and how to use it properly.
Step 4: Monitor and Review
The last step in the FLHA process is often the most neglected, but it’s the one that ensures everything else holds together. Once control measures are in place, they must be monitored regularly and adjusted as needed.
Conditions change—weather shifts, equipment degrades, teams rotate, and tasks evolve. What was once an effective safeguard may no longer be enough.
Regular reviews should check:
- Whether engineering controls (like barriers or ventilation systems) are functioning properly
- If administrative practices (like work schedules or signage) are still being followed
- Whether PPE is being used correctly, and if replacements are needed
- If workers feel confident that the current controls are working
Also look at safety indicators like incident frequency, near-miss trends, and absenteeism. Are hazards recurring? Are new ones appearing? Use this data to refine your hazard controls and update your FLHA protocols.
It’s also essential to run FLHAs at key trigger points, such as:
- The beginning of a shift
- After a break or change in work sequence
- When a new worker joins the crew
- After equipment failures or unusual events
- When environmental conditions change
Digital communication tools like Yourco can help notify workers of changes instantly, share FLHA updates in real time, and even collect on-the-ground feedback via SMS
When FLHAs are done consistently and thoughtfully, they become a natural part of how your team works—not just a safety form. They build awareness, encourage communication, and create a shared sense of responsibility for safety. Over time, they shift your culture from reactive to proactive, reducing risk while improving morale and productivity.
Safety That Works: Putting It All Together
Field Level Hazard Assessments are one of the most effective tools available for preventing workplace incidents and maintaining compliance. But their real value comes from how they are executed. When FLHAs are done thoroughly and consistently, they bridge the gap between high-level safety plans and the realities workers face on-site. A successful FLHA process relies on active hazard identification, clear risk assessment, tailored control measures, and ongoing monitoring. It also depends heavily on communication—making sure that the right information reaches the right people at the right time.
This is where many organizations fall short. Even well-designed safety programs can break down if frontline workers never see the updates, can't report hazards in real time, or are excluded from the safety loop because of language or location. For teams spread across job sites, working irregular shifts, or constantly adapting to changing conditions, communication becomes the linchpin of workplace safety.
Yourco solves this problem by removing the barriers that traditionally limit safety communication. As an SMS-based employee app, it allows safety managers to reach every worker directly on their mobile phone, without requiring internet access, app downloads, or company email accounts. Whether it’s a shift-start reminder, a safety alert, or a request for hazard feedback, Yourco ensures that messages are seen and acted upon. With a 98 percent read rate and support for over 135 languages, it closes the communication gap for workers who are often overlooked by conventional systems.
Yourco also supports two-way communication, making it easy for employees to report new hazards or unsafe conditions from the field. A worker can spot an issue, snap a photo, and send it directly to the safety team within seconds. This kind of immediate reporting helps organizations act on problems before they escalate and fosters a culture where safety is everyone's responsibility. Because all communications are logged and searchable, documentation becomes easier, audits are more transparent, and safety data is always within reach.
Yourco’s analytics layer gives you a real-time view into safety conversations across locations. They can track which job sites are generating the most hazard reports, identify where safety protocols are working or breaking down, and see which regions need more training or process improvements. Whether you're managing a single facility or dozens nationwide, Yourco turns frontline feedback into actionable insight, helping you allocate resources and strengthen your FLHA program where it’s needed most.
For HR managers and safety leaders committed to building stronger FLHA programs, Yourco offers a practical way to support every stage of the process. From hazard alerts to follow-up messages and form distribution, it helps standardize communication, drive accountability, and improve response times. It’s not just about technology—it’s about enabling a safer, more responsive workplace where no message gets lost and no worker is left behind.
Try Yourco for free today or schedule a demo and see the difference the right workplace communication solution can make in your company.