Time and Attendance Made Easy: Best Systems for Manufacturing Operations

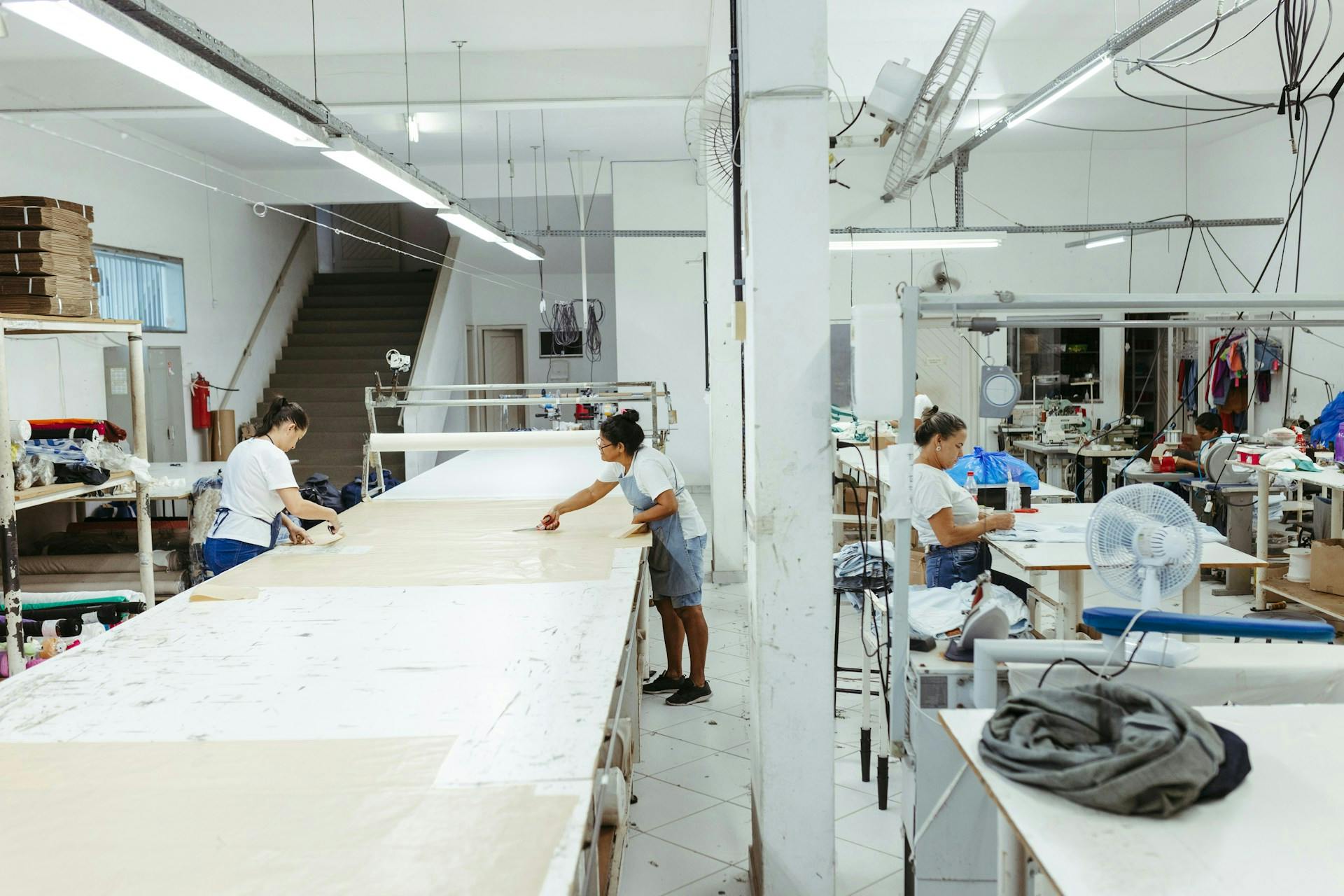
In industrial environments, traditional tracking methods often fall short, especially in complex manufacturing settings with multiple shifts and evolving compliance demands. Time and attendance systems play an important role in addressing these gaps by improving visibility, streamlining shift coordination, and supporting regulatory adherence.
Many manufacturers face persistent challenges, including manual processes that lead to inaccurate records, varied shift patterns, limited real-time data, and compliance risks tied to overtime and break policies.
These issues can also impact employee trust when transparency is lacking. That’s because conventional tools often fail to deliver the insights needed for efficient workforce management. Fortunately, SMS-based platforms offer a practical solution, delivering real-time updates on any mobile phone—with read rates of up to 98%.
Key Benefits of Implementing Time and Attendance Systems for Manufacturing
Modern time and attendance systems bring major benefits to manufacturing operations, helping to enhance productivity in manufacturing. Here's a look at three core advantages these systems deliver:
Enhanced Accuracy
Automated systems drastically cut down human errors that plague manual tracking. Paper timesheets and outdated punch clocks create opportunities for buddy punching, wrong entries, and unreadable records. By digitizing the process, time and attendance systems help ensure that employees are accurately compensated for hours worked.
Accurate time tracking can also support incentive compensation strategies, by ensuring employees are fairly rewarded for their contributions. The improved accuracy also reduces administrative burdens on payroll departments who previously spent hours reconciling discrepancies between timesheets and actual work performed.
Many companies report fewer disputes and complaints related to payroll after adopting automated systems—boosting employee morale and trust. This, in turn, decreases time-consuming HR interventions and strengthens overall workplace satisfaction.
Compliance and Regulation Management
Manufacturing faces complex regulations including labor laws, union agreements, and industry standards. Automated time and attendance systems help maintain compliance and avoid costly penalties. Key compliance features include:
- Automatic enforcement of effective overtime policies,
- Tracking of required break periods,
- Management of working hours across different locations
- Detailed audit trails for regulatory compliance
Different rules often apply to different employee classes, shifts, or departments, making manual compliance nearly impossible at scale.
With proper configuration, these systems handle diverse compliance needs simultaneously, from tracking mandated rest periods to calculating overtime according to variable rules. They maintain comprehensive records useful during labor disputes or government audits, potentially saving thousands in fines and legal costs through consistent rule application.
With these features, manufacturing companies can also reduce the risk of costly violations and streamline compliance.
Operational Efficiency
The most significant advantage might be the overall improvement in operational efficiency. These systems help payroll, enhance workforce management, and provide insights for smarter decisions.
Modern systems also support proactive management practices through early detection of attendance patterns. Supervisors receive notifications about tardiness trends before they become serious problems. These practices not only improve efficiency but also increase employee engagement by addressing issues proactively.
By reducing administrative burden, managers gain more time to focus on high-impact activities such as training, planning, or optimizing workflows. Additionally, these systems help lower overtime expenses by improving schedule accuracy and reducing the risk of unplanned shifts. Real-time and historical data also empower organizations to optimize staffing levels across departments more effectively.
SMS-Based Solutions: A Modern Approach
While traditional systems offer great benefits, SMS-based platforms are emerging as a smart solution for manufacturing workforces. These systems use mobile phones to provide instant message delivery for clock-ins, clock-outs, and alerts, achieving high response rates.
SMS solutions address several manufacturing-specific challenges simultaneously. They work well in environments where computer access is limited or impractical. The minimal training requirements reduce barriers to adoption among diverse workforces, highlighting the importance of IT training in facilitating the adoption of new technologies. Many platforms also offer multilingual support, accommodating workforces with varying language preferences.
The instant nature of text messaging ensures time-sensitive communications reach workers promptly. Integration capabilities with existing systems mean these solutions complement rather than replace current infrastructure investments.
SMS-based platforms can also enhance multi-location efficiency by providing a consistent time-tracking solution across various sites. Additionally, SMS platforms can function as mass notification systems, delivering urgent updates swiftly to all employees. Through implementing solid time and attendance systems, manufacturers can increase accuracy, ensure compliance, and improve efficiency all at once.
Features of Effective Time and Attendance Systems for Manufacturing
When choosing a time and attendance system for manufacturing, certain features stand out as important. Here's what makes these systems truly effective:
Robust Scheduling Capabilities
Manufacturing often involves complex shift patterns, including rotating shifts, night work, and multi-site operations. Effective systems provide:
- Shift swapping mechanisms
- Overtime management
- Multi-site scheduling
- Temporary worker integration
These features help optimize your workforce and prevent production bottlenecks. Advanced systems also accommodate split shifts, where employees work multiple segments within a single day. Manufacturing environments require tools that handle varying skill requirements for different stations or machines.
Systems must track worker certifications and qualifications to ensure properly skilled employees are assigned to appropriate tasks. The best systems balance operational needs with employee preferences, reducing turnover while maximizing production capability.
Integration with Payroll and HR Systems
Seamless connection between time data and payroll/HR systems is important for efficiency and accuracy. Key integration options include: API-based integration for real-time data sync, file transfers for scheduled data exports, and direct integration modules within HRIS suites.
These integration methods eliminate manual data entry, reduce errors, and speed up payroll. Integration capabilities extend beyond simple data transfer, allowing sophisticated interactions between systems. Holiday calendars automatically sync between platforms to ensure accurate pay calculations.
Employee status changes propagate through connected systems without duplicate entry. Well-integrated systems also provide audit trails showing exactly when and how time data is transferred to payroll, simplifying compliance verification and troubleshooting efforts.
Advanced Reporting and Analytics
Modern systems provide powerful reporting tools that offer insights into: labor costs, productivity trends, and attendance patterns. Features to look for include: real-time dashboards, automated alerts for absenteeism, and analytics for data-driven decisions.
Real-time tracking allows more efficient staff planning and more accurate cost estimates, important for managing output and labor expenses in manufacturing. Cloud capabilities and real-time tracking are also considered "must-have" features for modern, scalable manufacturing systems.
The analytical power extends to predictive capabilities, forecasting staffing needs based on historical patterns. Custom report builders allow managers to create personalized views showing exactly what they need without IT assistance.
Many systems offer exception reporting that highlights outliers rather than requiring review of all data. Comparative analytics help benchmark performance across departments, shifts, or facilities. Visualization tools transform complex data into accessible charts and graphs that reveal patterns instantly. The best systems export data to business intelligence platforms for deeper analysis alongside other operational metrics.
Overcoming Challenges with Time and Attendance Systems
Manufacturing environments create unique challenges for time and attendance tracking. Most manufacturing workers don't sit at desks—they work on shop floors, production lines, or across multiple facilities without regular computer access. This makes traditional tracking methods fall flat. Modern solutions tackle this problem through:
- SMS-Based Solutions: These use phones for clock-in/out and work effectively since they function on any mobile phone without internet or special training. What makes this even more powerful is the analytics layer: every clock-in, absence, or alert generates data that can be analyzed to surface attendance trends, late shift patterns, or locations with frequent scheduling gaps. This gives operations and HR teams actionable insights to improve workforce planning, address potential compliance issues, and boost overall productivity across sites.
- Biometric Systems: Fingerprint scanners or facial recognition provide accurate identification and stop "buddy punching."
- RFID and Contactless Options: RFID badges or contactless check-ins make the process quick and easy, perfect for places where hygiene and speed matter.
Managing Compliance in Manufacturing
Manufacturing faces tough compliance requirements, like:
- Complex union agreements
- Strict labor laws
- Different rules for multi-site operations
Modern time and attendance systems help manage these challenges through:
- Compliance Checks: Systems can enforce overtime rules, break periods, and working hours across different locations.
- Detailed Audit Trails: Complete logs of all time activities support regulatory compliance and protect you during audits.
- Integration with Payroll: Direct connection with payroll systems ensures accurate wage calculations, including complex overtime and shift differential rules.
With these features, manufacturing companies can reduce the risk of costly violations and streamline compliance. Integrated systems provide real-time visibility into workforce data, allowing quick response to attendance issues and better scheduling to maintain compliance.
Advanced systems automatically document required safety procedures or mandatory training. Some platforms include attestation features where employees confirm break compliance through digital signatures. Compliance reporting simplifies government-mandated documentation like EEO reports.
Selecting the Right Time and Attendance System
Finding the perfect time and attendance system for your manufacturing operation means focusing on features that address your specific challenges. Two important criteria stand out:
Scalability and Customization
Manufacturing companies need systems that grow with them and adapt to their unique needs. Look for solutions that support:
- Multiple locations and departments
- Custom groups for different production lines or teams
- Flexibility for various shift patterns and overtime rules
- Ability to handle different regional requirements for international operations
Truly scalable systems allow adding users without performance degradation as companies grow. Customization capabilities should extend to creating company-specific approval workflows that match organizational hierarchies. Manufacturers with seasonal fluctuations need systems handling temporary workers efficiently.
Growing operations benefit from platforms supporting staged rollout across facilities. Multi-entity organizations require consolidation capabilities while maintaining separation between business units. Forward-thinking companies choose systems with API access allowing future integration with evolving technologies.
The most adaptable solutions permit field customization so administrators can add tracking elements without vendor intervention. Robust systems also accommodate different pay rules for various employee classifications while maintaining a cohesive reporting structure.
User-Friendly Interface
In manufacturing, where technology adoption can be challenging, a simple interface makes all the difference. Focus on systems offering:
- Clear, easy-to-navigate dashboards for supervisors
- Straightforward clock-in/out processes for workers
- Minimal training requirements
SMS-based systems use familiar texting interfaces that require no training, making them ideal for manufacturing workforces.
Administrative screens should organize functions logically, placing common tasks prominently. Mobile interfaces must remain functional on various device sizes for supervisors moving throughout facilities. Employee-facing components should minimize required steps while maximizing accuracy.
Multi-language support assists diverse workforces, improving adoption rates. Well-designed systems include contextual help features answering common questions without contacting support. Thoughtful implementations incorporate user feedback mechanisms for continuous improvement. Graphics and visuals should supplement text instructions for workers with limited reading proficiency or language barriers.
Beyond these core needs, consider: hardware durability, security features, vendor support, implementation speed, and total cost. When evaluating systems, think about your specific operation's needs, size, and complexity.
Comparing Leading Systems
When choosing a time and attendance system for manufacturing, you need to understand the different options available. Here's a breakdown of the main types and what they offer:
Traditional Hardware-Based Systems
These include biometric scanners, RFID cards, and punch clocks—known for reliability and security in tough environments.
Advantages:
- Hold up well in harsh industrial settings
- Strong security features to prevent time theft
- Work in places without consistent internet
Limitations:
- Less flexible reporting
- May need more maintenance due to physical wear
These systems typically store data locally before transmitting to central databases, ensuring continuous operation during network outages. Hardware durability becomes particularly important in environments with temperature extremes, dust, or moisture.
Manufacturers often prefer physical systems in high-security settings where employee identity verification is paramount. Some facilities with multiple entry points distribute collection terminals strategically to minimize time spent traveling to clock stations.
Installation requires physical mounting and electrical connections, sometimes necessitating facility modifications. Replacement parts and repair services factor into long-term cost calculations beyond initial purchase price.
SMS-Based Platforms
These give flexibility for workers without needing special hardware or apps.
Benefits:
- Extremely accessible (98% read rate for SMS)
- No specialized hardware needed
- Works on any phone, even without internet
These systems excel in environments with limited technology infrastructure or diverse workforce technical abilities. Text-based interfaces eliminate login credentials that workers might forget. Implementation typically takes days rather than weeks or months. Cellular coverage replaces internet connectivity requirements, important in facilities with reception dead zones.
Organizations save significantly on hardware costs since employees use their existing phones. Character limits in text messages encourage concise, clear communications. Many platforms include intelligent response processing that interprets various reply formats correctly.
Some solutions incorporate photo verification capabilities for identity confirmation. Attendance verification codes can prevent off-site clock-ins when physical presence matters.
Cloud-Based Solutions
These modern, software-focused systems offer remote access, automatic updates, and strong reporting.
Key Features:
- Access from anywhere for managers
- Software updates without IT involvement
- Advanced analytics and reporting
Potential Concern:
- Depends on internet connectivity
- Usually not user-friendly
- Low adoption rates with a non-technical workforce
Cloud solutions typically follow subscription models with predictable monthly costs rather than capital expenditures. Data security responsibility shifts largely to vendors who maintain sophisticated protection measures. Implementation happens faster than hardware installations since physical equipment requirements remain minimal.
System availability depends on both internet reliability and vendor uptime guarantees. Mobile apps often accompany cloud platforms, extending functionality to smartphones and tablets. Geofencing capabilities can restrict clock-in capabilities to approved locations.
Data backup and disaster recovery typically come standard with reputable providers. Bandwidth requirements matter for facilities with limited connectivity options.
Enterprise-Grade Integrated Suites
These comprehensive systems combine time tracking with scheduling, payroll, and HR management.
Advantages:
- All-in-one solution for workforce management
- Powerful capabilities for complex operations
Consideration:
- Higher cost and more complex implementation
These platforms typically deliver robust compensation management capabilities beyond basic time tracking. Advanced workflow configuration allows modeling complex approval hierarchies. Sophisticated reporting spans multiple human resource functions for comprehensive workforce analytics.
Role-based access controls ensure appropriate information visibility at different organizational levels. Implementation typically requires significant configuration to match organizational processes. Integration capabilities extend beyond HR systems to production planning and ERP platforms.
Many suites offer employee self-service portals for accessing personal information. Training requirements exceed simpler solutions due to comprehensive functionality.
Transform Your Workforce Connection Today!
Time and attendance systems significantly improve manufacturing operations through increased accuracy, better compliance, and improved efficiency—often with rapid return on investment. Modern SMS-based platforms address manufacturing's challenges without complex tech or extensive training. Using existing mobile phones, these systems create accessible tracking alternatives to traditional methods. Automated systems reduce errors, simplify payroll, maintain compliance, and provide real-time labor insights.
Yourco's SMS-based platform connects non-desk manufacturing workers through simple text messaging—no downloads required. Achieving nearly perfect engagement rates, Yourco integrates with existing systems to create a complete workforce management solution that improves efficiency while maintaining compliance.
Yourco also has the analytics layer behind every interaction. From clock-ins and safety alerts to missed shifts and training reminders, Yourco captures real-time data and translates it into actionable insights—helping leaders identify patterns in attendance, safety risks, communication gaps, and team responsiveness across locations. This enables better decision-making and continuous improvement on the frontline.
Beyond time and attendance, Yourco offers a full suite of workforce communication tools tailored for manufacturing. Features like one and two-way messaging, multilingual support across 135+ languages, automated surveys and polls, and secure document sharing ensure that every employee stays informed, engaged, and empowered—no matter where they are. Yourco also provides enterprise-grade security, HRIS and payroll integrations, and flexible messaging options that allow leaders to manage communications across multiple locations with ease.
Try Yourco for free today or schedule a demo and see the difference the right workplace communication solution can make in your company.