Boost Engagement & Productivity Through Manufacturing Communication

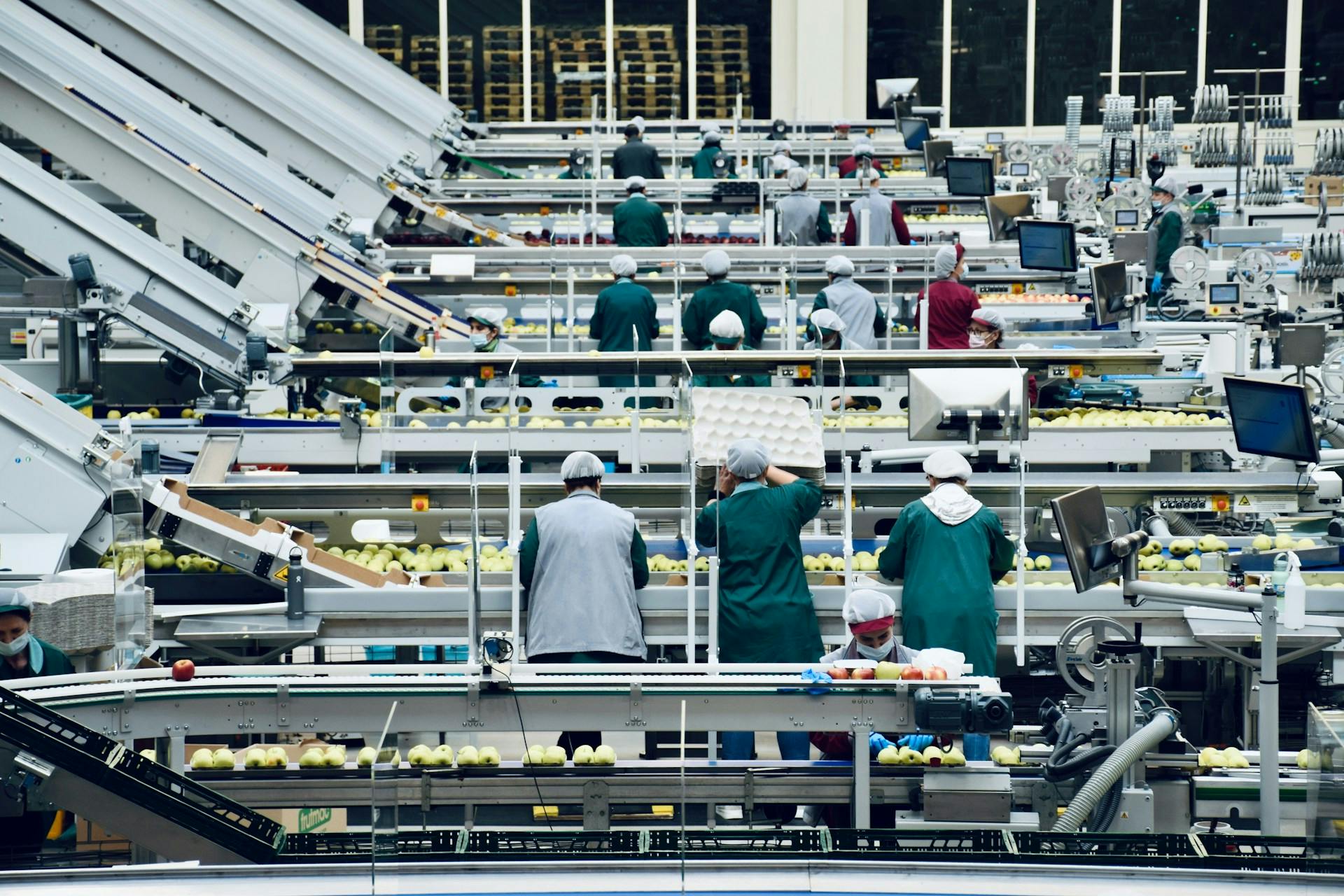
Manufacturing has always relied on precision, collaboration, and timing. Yet on today’s factory floors, one critical element often goes overlooked: the flow of information. Without clear and timely communication, even the best processes and equipment cannot perform at their highest potential. When frontline teams feel informed, connected, and aligned with company goals, the ripple effects are unmistakable; from safer workplaces to higher quality outputs and stronger employee morale.
Modern manufacturing is evolving, and so must the ways organizations connect with their workforce. In this article, we explore how improving manufacturing communication can unlock higher engagement, greater operational efficiency, and stronger business outcomes across the factory floor.
Why Is Manufacturing Communication Important?
Communication serves as the backbone of everything in manufacturing. Research from Gallup confirms that companies with connected employees experience 14% higher productivity and 81% lower absenteeism. When information flows properly in manufacturing communication, operations run smoothly. When it doesn't, the consequences hurt. One manufacturing study found that communication breakdowns contribute to approximately 70% of all operational errors.
Impact on Employee Engagement and Morale
Workers who feel informed feel valued. Those left in the dark disengage quickly. Manufacturing communication acts as an "alternate currency"—when money can't motivate any further, information sharing picks up the slack.
Manufacturing workers particularly value being "in the loop" about changes affecting their daily work. When communication falters, trust erodes quickly, creating a cycle of disengagement that's tough to reverse. Management teams can rebuild this trust through consistent, transparent messaging about organizational changes, production goals, and company performance.
Regular updates on business health help frontline workers connect their daily efforts to broader company success, reinforcing their value to the organization and strengthening their commitment to quality and productivity.
Operational Efficiency and Safety
Clear manufacturing communication directly impacts the bottom line. Companies with effective communication strategies experience fewer safety incidents and higher productivity.
Picture what happens when a process change isn't properly shared: Workers follow outdated procedures, quality drops, and rework becomes necessary. Similarly, when safety protocols aren't clearly conveyed, accidents increase.
The link between manufacturing communication and downtime is just as significant. Research from Aberdeen Group reveals that manufacturers with strong communication practices experience 47% less unplanned downtime than those with poor information flow.
This connection extends to inventory management, where accurate, timely communication between production, warehousing, and procurement teams reduces excess inventory costs and prevents stockouts. Clear communication is equally essential for equipment upkeep.
Companies that implement structured communication protocols for machine maintenance and enforce Standard Operating Procedures (SOPs) often report equipment lifespan increases, representing substantial cost savings across large facilities.
SOP-driven communication ensures that maintenance schedules, troubleshooting guidelines, and compliance checks are consistently followed, minimizing downtime and preserving asset value.
Challenges in Manufacturing Communication
Manufacturing environments create unique communication obstacles that office-centric solutions simply can't address, requiring specialized communication strategies for deskless workers.
Reaching Workers without a Desk
The digital divide cuts straight through factory floors. While corporate staff stay connected through email and company intranet, over 83% of the frontline workforce don’t have a corporate email address, and 45% lack access to the company intranet during work hours.
This disconnect creates a dangerous information vacuum often filled with unofficial channels. These unofficial channels lead to version control issues where workers might receive conflicting information about procedures or safety protocols. Companies attempting to combat this trend with traditional solutions like increased bulletin board postings or more frequent shift meetings find these methods insufficient for time-sensitive updates.
Additionally, the physical nature of manufacturing work often prevents employees from checking traditional communication points during their shifts, further delaying information reception.
Multilingual and Multi-Location Barriers
Modern manufacturing workforces span multiple languages, cultures, and locations—sometimes within a single facility. According to the Bureau of Labor Statistics, as of 2024, about 19.4% of the total employed population is Hispanic or Latino, a demographic more likely to speak a language other than English at home.
This linguistic diversity creates serious safety risks when important information isn't understood. The Occupational Safety and Health Administration (OSHA) estimates that language barriers are a contributing factor in 25% of job-related accidents. Addressing multilingual communication in manufacturing is important for mitigating these risks.
The multi-shift nature of manufacturing makes these challenges worse. Information shared with day shift workers often fails to reach night crews, so they often report feeling isolated from company culture and overlooked in communication strategies.
Manufacturers with multiple facilities face additional complications when headquarters communications must flow through local management layers, often causing delays and message distortion as information passes through several intermediaries before reaching frontline staff.
Strategies for Effective Manufacturing Communication
Smart manufacturers are adopting targeted approaches to bridge these manufacturing communication gaps.
Implementing Mobile and Real-Time Communication Tools
Implementing effective communication tools for deskless workers, such as mobile-first solutions, meets manufacturing workers where they are—on the production floor with their personal devices. According to Pew Research, 98% of Americans own a cellphone of some kind, making mobile the most accessible communication channel.
SMS-based platforms excel in manufacturing environments. They need no app downloads, use minimal data, and work on any phone—from basic feature phones to smartphones. Text messages have a 98% open rate compared to just 20% for emails, making SMS for manufacturing communication highly effective.
Leading manufacturing communication platforms provide dedicated toll-free numbers to remove cost barriers for employees. In addition, manufacturing facilities implementing tools like a mass texting service for business report significant improvements in response time to production issues and maintenance requests.
Text-based communications also allow workers to receive messages while wearing required PPE, a major advantage over solutions requiring screen interaction or login credentials.
Additionally, the asynchronous nature of text messaging ensures information reaches workers across different shifts without requiring additional staff to deliver the message in person. This proves especially valuable for weekend shifts and overnight operations where management presence may be limited.
Real-world applications include:
- Shift Reminders
- Instant shift change notifications
- Organizational Changes
- Emergency alerts and safety updates
- Production goal announcements
- Machine status updates
- Training reminders
- Gathering Employee Feedback
Establishing One-Way and Two-Way Communication Channels
Manufacturing teams thrive with robust two-way communication systems that empower workers to contribute ideas and feedback, thereby helping to improve frontline employee engagement.
Effective two-way systems include:
- Unlimited Outgoing & Incoming Messages
- Message Segmentation
- AI-Powered Automatic Translations
- Polls & Surveys
- All communications are logged and searchable for audits and compliance
Companies employing bidirectional communication discover previously hidden inefficiencies in processes through frontline worker input. Manufacturing teams particularly benefit from allowing all staff levels to report quality concerns through accessible channels, creating an early warning system for potential issues before they affect finished products. Two-way systems also strengthen safety cultures by reducing barriers to reporting hazards.
Workers feel empowered to share observations knowing they have direct access to appropriate decision-makers rather than relying on information to travel through traditional hierarchical channels.
At the same time, structured one-way communication remains essential for keeping the entire workforce aligned on urgent updates, shift changes, and company-wide announcements. Successful manufacturing communication programs combine company-wide one-way messaging to reach every employee with localized two-way communication at the site level, ensuring both broad consistency and local responsiveness.
Leveraging Technology for Multilingual Communication
Modern communication platforms incorporate real-time translation capabilities. Leading solutions offer instant translation into multiple languages, ensuring manufacturing communication reaches everyone regardless of language background.
While using technology is important, understanding the cost and benefits of using professional translation services can also play a significant role in effective communication. Smart implementation includes:
- Language preference selection during onboarding
- Human review of machine translations for communications
- Supplementing text with universal symbols and visuals
- Offering information in the most common languages at each facility
Beyond safety improvements, multilingual communication significantly affects quality metrics and team cohesion. Manufacturing facilities with language-inclusive communication report stronger cross-cultural teamwork and improved knowledge sharing between work groups that previously operated in siloed language communities.
The inclusion of all languages in official company communication also decreases dependence on unofficial translators within the workforce, reducing the risk of message distortion and ensuring everyone receives the same information directly from management.
Building an Inclusive Manufacturing Communication Environment
Technology alone won't solve manufacturing communication challenges. Success requires analyzing workforce needs and building inclusive communication cultures. Building an inclusive communication environment requires a focus on internal communications.
Understanding Your Audience and Infrastructure
Before implementing new communication tools, smart manufacturers conduct communication audits.
Effective audits include:
- Workforce communication preference surveys
- Technology access assessments
- Language and literacy mapping
- Shift pattern analysis
- Physical workspace communication flow mapping
Communication environment assessments often reveal surprising information gaps. For instance, many manufacturing facilities discover during audits that workers rely heavily on informal tribal knowledge rather than documented procedures because formal documentation is inaccessible during shifts. Understanding these existing information flows helps companies design solutions that complement rather than disrupt established patterns.
Manufacturers benefit from mapping not just digital infrastructure but also the physical environment where communication occurs—noting high-traffic areas, existing message boards, and natural congregation points where workers already exchange information informally.
Creating Communication Plans with Flexibility
Effective manufacturing communication relies on thoughtful planning rather than ad-hoc messaging. The most successful plans include:
- Multi-channel approaches that don't rely on a single method of communication (eg. SMS for immediate and instant contact and digital signage and bulletin boards as reminders)
- Balance between company-wide and location-specific messaging
- Redundancy for communications
- Clear escalation paths for urgent information
- Appropriate frequency guidelines to prevent information overload
Smart manufacturers also recognize different information needs across roles. Line workers prioritize immediate operational information, while team leads need both operational and strategic content. Facility-specific content resonates more strongly with manufacturing teams than corporate-wide communications, suggesting localization increases engagement.
Manufacturers with successful communication systems develop contingency plans for system outages, recognizing that technology failures can occur during times when communication becomes most necessary, such as emergencies or major production changes. The most effective programs include scheduled review cycles where communication plans adapt based on workforce feedback and changing operational needs.
Measuring and Improving Manufacturing Communication Impact
What gets measured gets improved. Manufacturing leaders increasingly track communication effectiveness and tie it to operational outcomes.
Setting Benchmarks and Goals
Successful communication initiatives start with clear objectives. Research from Deloitte found that companies with defined communication metrics see 26% higher ROI from their communication investments.
Effective manufacturing communication metrics include:
- Safety incident reductions
- First-time quality improvements
- Production schedule adherence
- Employee satisfaction scores
- Reduced time-to-resolve issues
- Training completion rates
Smart manufacturers establish baseline measurements before implementing new communication strategies, enabling meaningful before-and-after comparisons. Manufacturing teams benefit from connecting communication metrics to existing performance tracking systems rather than treating communication as a standalone initiative.
This integration helps demonstrate direct relationships between information flow and operational results. Department managers who set specific communication goals tied to their area's performance indicators show greater commitment to communication improvement initiatives.
For example, maintenance teams might track mean-time-to-repair reductions resulting from faster information flow, while production teams monitor scrap reduction resulting from more consistent process communications.
Utilizing Analytics for Continuous Improvement
Modern communication platforms provide rich analytics that demonstrate impact. Manufacturing companies using data-driven communication approaches report 23% higher workforce productivity.
Key metrics to track include:
- Message open rates by shift, department, and location
- Response times to updates
- Feedback volume and quality
- Information flow through management layers
- Correlation between communication metrics and production outcomes
Advanced manufacturing communication systems also enable A/B testing of different message formats and timing to determine which approaches generate the strongest response rates. In addition, communication analytics reveal unexpected patterns, such as certain departments or individuals acting as information bottlenecks where message transmission slows or stops completely.
Manufacturing facilities using message tracking capabilities can verify that important information reaches its intended recipients rather than assuming message delivery.
Transform Your Manufacturing Communication Now
The manufacturing communication gap isn't just inconvenient—it creates real operational risks that affect safety, quality, and workforce stability. As we've seen, maintaining strong connections with frontline employees is no longer optional. It is essential for ensuring production runs smoothly, goals stay on track, and teams stay engaged.
Yourco provides the complete communication solution manufacturing teams need to bridge these gaps. Built specifically for the non-desk workforce, Yourco enables manufacturers to reach every employee, regardless of technical ability, location, or device limitations. By using the simplicity and reliability of SMS messaging, Yourco ensures critical updates about shift changes, safety alerts, production targets, and company announcements reach workers instantly and without friction.
Beyond basic messaging, Yourco strengthens communication strategies with real-time multilingual translation capabilities, helping companies communicate clearly across diverse workforces. Employees receive messages in their preferred language automatically, improving understanding and reducing the risk of costly miscommunication. With Yourco, manufacturing leaders can send one-way corporate updates to the entire organization, ensuring consistency at the company level, while also enabling two-way communication at individual sites to capture frontline feedback, address issues quickly, and maintain local agility.
All communications are logged and searchable, creating an audit-ready record that supports safety initiatives, compliance efforts, and operational transparency. Meanwhile, built-in analytics provide actionable insights, helping leaders track message engagement, identify communication bottlenecks, and continuously improve the way information flows throughout the organization.
By combining accessibility, flexibility, and intelligence into a single platform, Yourco transforms manufacturing communication from a daily challenge into a competitive advantage. In an industry where missed messages can directly impact the bottom line, Yourco ensures that every worker stays informed, engaged, and aligned with your company's mission.
Try Yourco for free today or schedule a demo to see firsthand how the right workplace communication platform can strengthen your operations and support your frontline teams.