From Chaos to Order: How Digital Work Instructions Streamline Operational Workflows

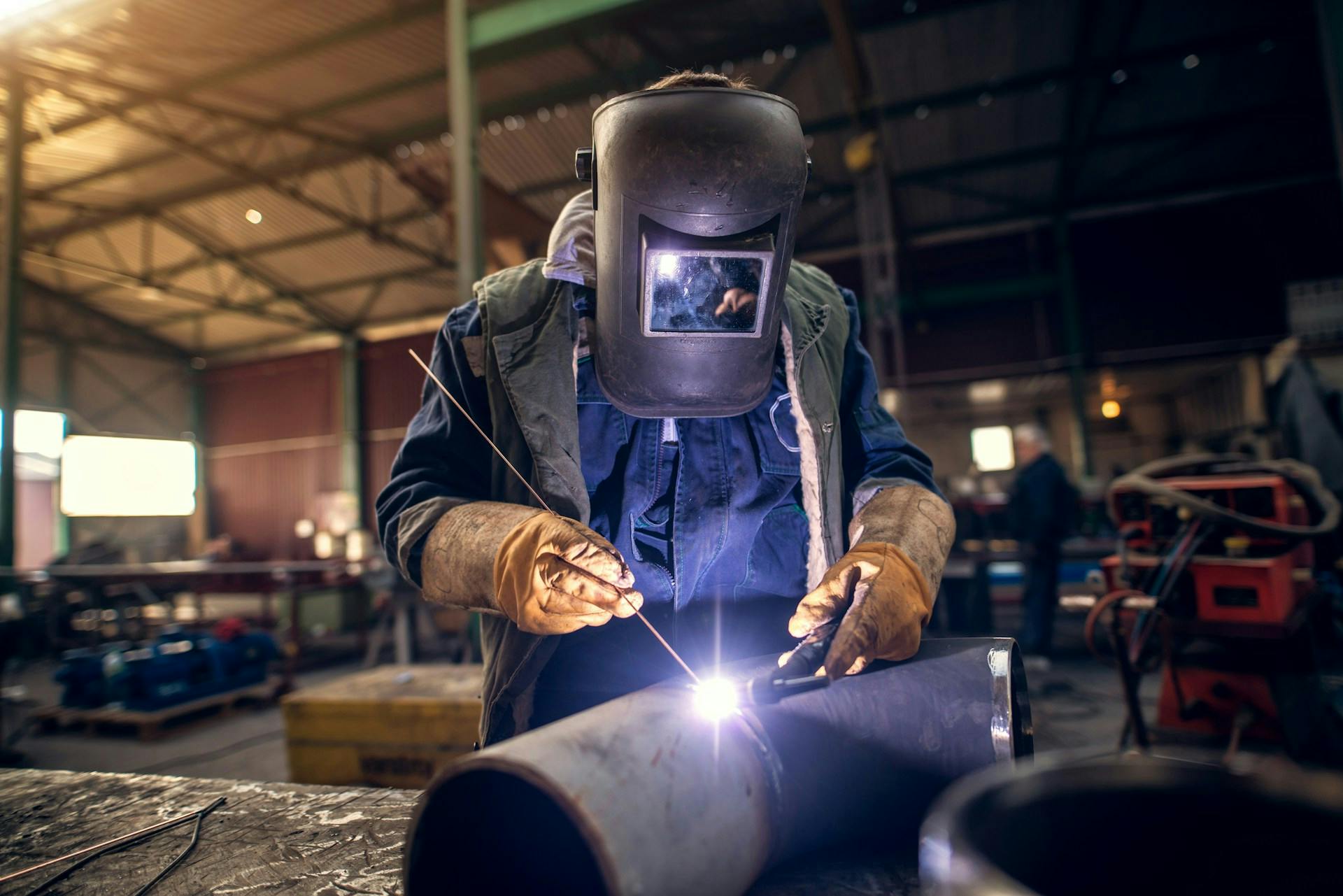
Transitioning from chaotic, outdated paper manuals to streamlined operational workflows is no simple task. For industries navigating increasing complexity and a diversifying workforce, operational efficiency hinges on clear and effective communication. Traditional work instructions, though familiar, often fail because they're static, cumbersome, and quickly outdated.
Digital work instructions, on the other hand, offer a dynamic solution by providing multimedia-rich, interactive guides that remain up-to-date at all times. But there's a catch: operationalizing these tools can be challenging, particularly among workers who may not be digitally savvy.
This article explores exactly how digital work instructions transform operational workflows from chaos to order and how using an SMS-based communication platform may be the best solution as it provides just the right type of middle ground for digital communication.
The Importance of Digital Work Instructions
Digital work instructions have become fundamental components of Industry 4.0 environments. As manufacturing and industrial settings embrace digital transformation, these electronic guides address significant challenges and transform workplace operations, helping to improve productivity.
Error Reduction and Quality Improvement
Digital work instructions minimize errors and enhance quality in manufacturing environments. They offer precise, step-by-step guidance with visual aids that simplify complex procedures. The digital format also incorporates interactive elements, videos, and 3D models that improve comprehension and prevent misinterpretation that commonly occurs with traditional documentation.
Furthermore, workers receive exactly what they need to perform tasks correctly the first time, significantly reducing the likelihood of mistakes during complex assembly or maintenance procedures.
The immediate accessibility of digital instructions also helps workers quickly reference procedures when questions arise, rather than proceeding with uncertainty or making assumptions that lead to quality issues.
Accelerated Training and Onboarding
Digital work instructions prove invaluable for workforce development and form a key component of employee onboarding strategies. These tools speed knowledge transfer and improve retention, resulting in faster completion times and fewer mistakes during the learning phase.
Digital instructions address labor shortages and skills gaps effectively. New employees become productive more quickly through interactive, detailed guidance that reduces training time while improving results, forming an essential part of a structured onboarding process. This advantage becomes especially important when experienced workers retire, taking decades of institutional knowledge with them.
The visual nature of digital instructions matches how younger workers prefer to learn, incorporating engagement strategies that increase information retention compared to traditional training methods.
Companies report significant reductions in time-to-proficiency for new hires after implementing digital work instructions, allowing them to maintain productivity despite workforce changes. The ability to include quizzes and checkpoints within digital instructions also helps trainers verify comprehension before advancing to more complex tasks.
Knowledge Retention and Standardization
Digital work instructions function as centralized repositories of operational knowledge, preserving best practices when experienced employees depart. This centralization ensures consistency across multiple locations or teams—an important factor for maintaining quality and operational efficiency across an organization.
The instant update and distribution capabilities represent a significant advantage. When processes change, digital instructions update immediately, ensuring all workers access current information. This flexibility matters in industries where regulations or best practices evolve continuously.
Manufacturing facilities with multiple shifts and locations particularly benefit from this standardization, as all workers follow identical procedures regardless of when or where they work. The centralized management of digital instructions also simplifies compliance requirements, as updates to meet new regulations can be quickly implemented and verified across the organization.
Additionally, the ability to include troubleshooting guides and common issue resolutions within digital instructions helps less experienced workers resolve problems independently, reducing the need for supervisor intervention.
Digital instructions also help diverse workforces overcome language barriers. Visual elements and translations bridge communication gaps in multilingual teams. This proves especially important since 81% of manufacturing employees aged 25-34 find text-heavy documentation challenging due to language diversity and varying reading skills.
Characteristics of Effective Digital Work Instructions
Digital work instructions have become necessary tools for guiding non-desk workers through complex tasks. To make a difference in operations and quality, these instructions need specific features that support diverse work environments and foster effective communication.
Visual and Interactive Content
Superior digital work instructions include interactive 3D models that demonstrate assembly sequences from multiple angles, allowing workers to manipulate views as needed. Step-by-step visual guides break complex tasks into manageable sections with clear progression indicators.
Video tutorials also showcase proper techniques performed by experienced workers, capturing nuances difficult to explain in text.
These visual approaches accommodate different learning styles and language proficiencies, making instructions accessible to everyone regardless of background. Color-coding and icons further enhance comprehension by creating visual shortcuts to important information like safety warnings or quality checkpoints.
When implemented thoughtfully, these visual elements reduce training time while simultaneously improving task completion accuracy across all experience levels.
Accessibility and User-Friendly Design
Effective digital work instructions must remain available whenever and wherever workers need them, requiring designs compatible with various devices including tablets, smartphones, and wearables.
Important accessibility features include responsive designs that adapt to different screen sizes without losing functionality or requiring constant zooming. Offline capabilities also ensure instructions remain available in areas with poor connectivity, such as remote facilities or basement levels with signal interference.
Intuitive navigation systems help workers quickly locate specific information without extensive searching, using clear categorization and search functionality. Cross-platform compatibility ensures instructions work correctly regardless of the operating system or device type used.
Adjustable text sizes and audio options accommodate workers with different visual abilities or learning preferences. Finally, the most effective systems remember individual user preferences and history, allowing workers to quickly return to frequently accessed instructions or bookmarked sections, further reducing time spent searching for information instead of completing tasks.
Real-Time Updates and Feedback Mechanisms
Effective digital systems include real-time update capabilities, ensuring workers always access the latest procedures and safety protocols. Two-way communication systems allow workers to provide feedback on instructions, report issues, suggest improvements, and receive timely answers to questions.
These feedback channels capture valuable insights from those closest to the work, identifying unclear instructions or opportunities for process improvement. Analytics tracking which instructions receive the most views or questions helps companies prioritize improvement efforts. Version control systems maintain instruction history, allowing comparison between iterations to understand how processes evolved.
Automatic notifications also alert workers when instructions relevant to their roles change, eliminating the risk of using outdated procedures. Integration with quality management systems creates closed-loop improvement processes where reported issues trigger instruction updates. Some advanced systems incorporate AI-powered analysis of user interaction patterns to identify potential confusion points before they cause problems.
Overall, the combination of current information and active feedback loops creates instruction systems that evolve alongside workplace needs.
Key Technologies Enhancing Digital Work Instructions
Digital work instructions continue improving thanks to advanced technologies that transform how workers receive guidance, perform tasks, and maintain safety. Three technologies stand out: Augmented Reality (AR), Artificial Intelligence (AI), and SMS-based employee platforms.
SMS-Based Employee Platforms
SMS-based employee platforms like Yourco significantly enhance digital work instructions, especially for non-desk, mobile, or distributed teams. Digital work instructions depend on immediate access, clarity, and timely communication—all strengths inherently provided by Yourco’s SMS platform. With a 98% open rate and an average response time of just 90 seconds, Yourco ensures critical instructions reach employees instantly, dramatically outperforming traditional channels like email, which typically see only 20% engagement.
Using Yourco, digital instructions become interactive through two-way messaging, enabling employees to quickly clarify instructions, provide immediate feedback, or report issues as they arise. This responsiveness significantly reduces errors, improves safety outcomes, and ensures instructions are clearly understood and promptly executed. Moreover, Yourco’s AI-powered translations across 135+ languages ensure digital instructions remain clear and accessible, regardless of language barriers within diverse teams.
Security and compliance are seamlessly embedded into Yourco’s handling of digital instructions. With robust security features, including end-to-end encryption, locked-file sending with PIN authentication, comprehensive message logging, and GDPR-compliant data management, sensitive operational guidelines remain protected. Additionally, detailed analytics and automated communication scheduling further optimize the effectiveness of digital instructions, enabling managers to proactively refine instructions based on real-time performance metrics and employee feedback.
The flexibility and scalability of Yourco’s SMS-based system ensure digital instructions align precisely with complex organizational structures. Location-specific and role-based messaging ensures instructions are relevant and timely for every employee. Detailed analytics such as attendance, compliance with instructions, and incident frequency allow continuous improvement of digital work instructions, enhancing operational efficiency and worker safety.
By integrating Yourco’s SMS platform with digital work instructions, organizations achieve clearer, faster, and more effective guidance, directly improving productivity, safety, and overall operational reliability.
Augmented Reality (AR) Applications
AR transforms how workers interact with their environment, placing digital information directly into the real world. This technology excels for complex tasks requiring precise visual guidance.
For example, AR-powered digital work instructions overlay 3D models directly onto equipment, providing guidance without making workers shift focus between task and manual. Workers see step-by-step visual cues superimposed on their actual work area, reducing errors and improving understanding. Remote experts can "see what the worker sees" and provide real-time guidance, improving collaboration and problem-solving.
The immersive nature of AR also creates stronger memory associations, helping workers retain procedures more effectively than through traditional learning methods. Maintenance technicians benefit from AR overlays that highlight specific components needing attention, eliminating confusion in complex machinery.
Assembly workers can view animated assembly sequences directly on their workstation, ensuring proper component orientation and sequence. Additionally, AR glasses enable hands-free operation, allowing workers to follow instructions while maintaining both hands on their task.
The technology also supports spatial anchoring, where instructions attach to specific locations in the physical environment, automatically presenting relevant information as workers move through different areas or workstations, reducing time spent searching for the right procedure.
Artificial Intelligence Integration
AI enables personalization and efficiency improvements in digital work instructions, creating more effective guidance systems.
Instructions adapt based on a worker's experience level, performance history, and real-time conditions, providing appropriate detail without overwhelming or underwhelming different skill levels. AI analyzes task data to identify improvement opportunities and optimize workflows, constantly refining procedures based on actual performance metrics.
Natural language processing enables voice-controlled instructions and real-time translation, breaking down language barriers in diverse workforces. Computer vision capabilities automatically detect errors or safety violations, alerting workers immediately before problems escalate. Machine learning algorithms identify patterns in worker interactions with instructions, highlighting areas where users frequently pause or make mistakes.
This data helps instruction designers improve unclear sections before they cause widespread issues. Predictive maintenance recommendations can be incorporated into work instructions based on equipment conditions, shifting from fixed schedules to need-based maintenance.
The combination of these capabilities creates instruction systems that continuously improve based on actual usage data, becoming more effective over time without requiring constant manual updates.
Powering Up Your Workforce: Why SMS is the Future of Digital Work Instructions
Digital work instructions deliver interactive guidance when needed, reducing errors while improving training effectiveness and productivity.
SMS-based platforms offer remarkable accessibility for frontline workers. Text messages reach workers regardless of location or device, making them ideal for time-sensitive updates and step-by-step guidance.
Yourco stands out as a purpose-built SMS employee platform that delivers work instructions directly to phones without requiring downloads. This approach works well to engage deskless workers who might not be tech-savvy but regularly use text messaging.
The platform enables two-way communication, allowing workers to ask questions and report issues—creating improvement loops that benefit everyone while standardizing operations and enhancing safety compliance. Utilizing effective communication tools like SMS platforms can greatly improve frontline worker engagement and productivity.
Try Yourco for free today or schedule a demo and see the difference the right workplace communication solution can make in your company.